技術トピックス - 切削工具トピックス -
インターナルブローチの刃付け研削について
ブローチの再研削時期を適切に選ぶことは、ワーク精度、ブローチ寿命を管理する上で最も重要です。ブローチが切れなくなってから続けてご使用されますと、摩耗は急速に進行し再研削量も多くなり様々なトラブルの原因となります。たびたび再研削を行い1回の再研削量を最小限にし、ブローチの切れ味を最良においた場合と比べると、1本のブローチの総切削個数(生産量)すなわち、ブローチ寿命には格段の差があります。
特にインターナルブローチの刃付け研削の場合は、ブローチ自体が細くて長いものが多く又、砥石の干渉がある等、他の切削工具と違った面があります。適切な刃付け研削を行うためのその要点についてご紹介致します。
刃付け時期
ブローチ | (1) 刃先に摩耗によるランドが白く見え始めた時 (摩耗幅0.05~0.1㎜未満) |
(2) 刃先に異常摩耗、チッピング、刃欠けを生じた時 | |
(3) 切粉が刃溝に圧着し始めた時 | |
(4) 切れ刃側面、二番面に切粉の溶着を生じた時 | |
ワーク | (1) 加工寸法が規格外になった時や、通りゲージが入らなくなった時 |
(2) 被削面の面粗さが悪くなった時 | |
(3) 切削終了時に過大に発熱した時 | |
ブローチ盤 | 引き抜き力が不当に増大した時 |
(初期の引き抜き荷重より30%増えた時) |
刃付け要領
- 1.ブローチはセンタに取付け、振れ止めを用いる。 (図1)
- 2.砥石径はブローチ径の2~3倍のものを使用する。
- 3.砥石の周速は1,300m/min以上を目安とする。
- 4.ブローチと砥石の中心を若干ずらす。 (図2)
- 5.砥石のセット角を求める。(注)
- 6.すくい角、刃底のRのチェックを専用ゲージを用いてチェックする。
- 7.切粉がスムーズに流れるように、すくい角と刃底部等に段がつかないようにする。
- 8.すくい面の面粗さは3.2S以下(目標1.6S)とする。
- 9.荒刃では、1刃の取り代を一定に保つため、荒刃全体の刃付け量を均一にする。
- 10.切れ刃に溶着があれば、刃付け前にあらかじめ油砥石などで手入れ除去しておく。
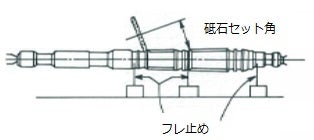
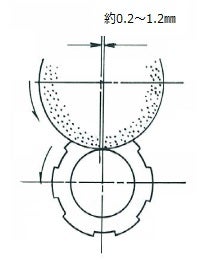
注)なお、刃付け時の砥石セット角は、刃付け盤に付属の『ブローチ直径・砥石径・すくい角』からセット角を導く早見表を参照願います。