加工事例 - 精密加工機の加工事例 - 小型精密加工機μV1
「撮像式工具測定システム」を用いた微細・精密加工
※本記事は、「型技術2011年7月号」に掲載した論文です。
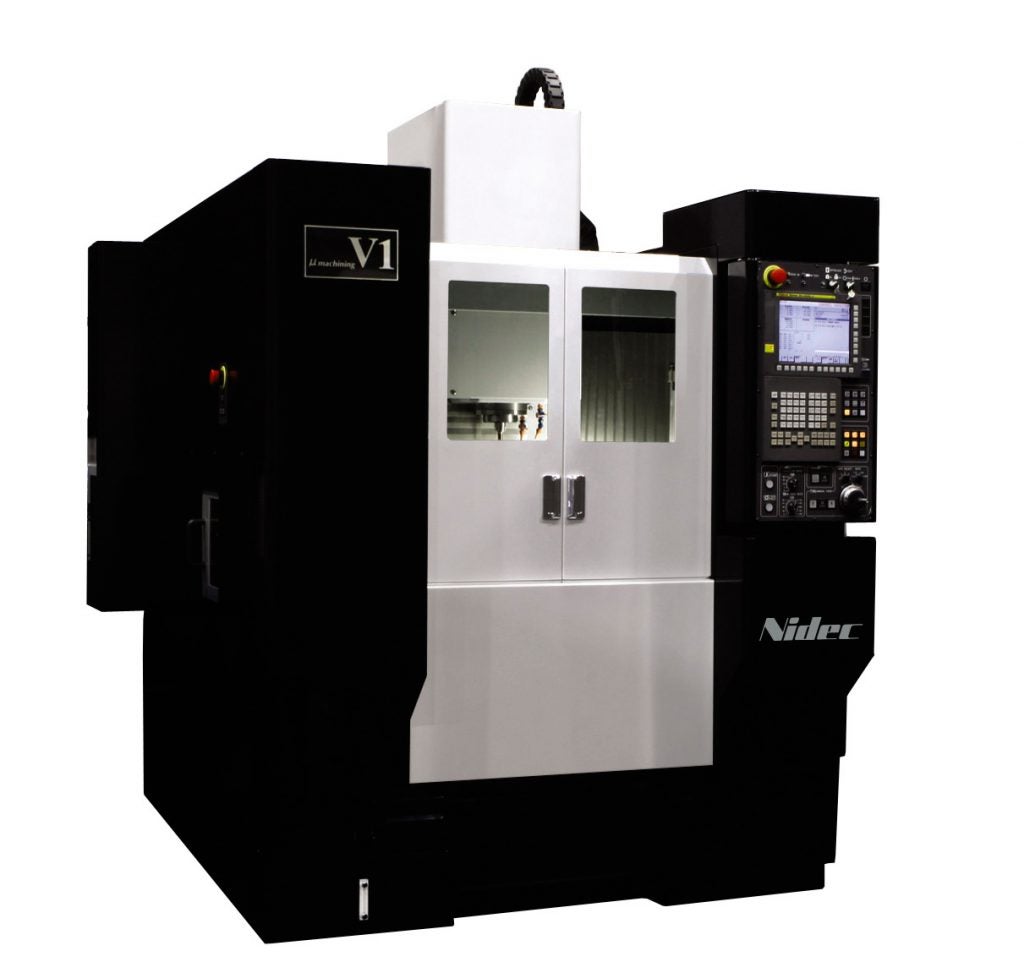
はじめに
IT、光学、医療機器、半導体デバイス等の部品の複雑化、高性能化に伴い、これらの部品や金型の加工の高精度化の要求が高まるとともに、表面テクスチャなどの微細形状加工も増えてきている。
当社においても、それらの要求に応えるため小型精密加工機μV1を用いて、微細・精密加工に取組んでいる。本稿では、その事例について紹介する。
微細・精密加工の問題点
微細・精密加工の障害となるのは、まず主軸や送りの振動、加工中の熱変位といった工作機械自体の運動精度の影響が挙げられる。これらが大きいと、寸法精度が維持できない、あるいは微細な形状が損傷してしまう恐れがある。
また、形状の微細化には工具に依存するところも大きく、現在は最小でφ10μmの工具まで市販されているが、このような極細工具は、従来の機上の工具測定装置では正確に測定できないという問題がある。従来の機上工具測定装置には、接触式のものとレーザー式のものがあるが、φ10μmの工具となると接触式ではタッチした衝撃で工具が折損してしまい、レーザー式ではレーザー光が10μmより大きいため遮光することができず、測定することができない。
更に、工具のみならずワーク側の機上測定も重要であり、特にワーク上面高さの測定に誤差があると、アプローチや初回の切込み時に食込んでしまい、工具折損してしまう場合がある。
μV1による解決策
当社μV1は、独自の主軸の潤滑・冷却方式により従来に無い低振動と低発熱を実現し、機械本体の剛性を高めて極めて高い安定性を確保している。
また、機上工具測定装置として「撮像式工具測定システム」を独自開発しμV1へ搭載している。撮像式工具測定システムは、LED照明と高解像度CCDカメラの間に工具を入れ、工具を撮像することにより工具を測定する(図1)。
このためφ10μmの工具であっても折損させることなく、0.1μm単位で測定することが可能である。加えて回転中の熱変位による刃先位置の変化を捉える機能があり、熱変位が安定してから工具長を取得し、熱変位量をキャンセルした上で、その後の安定した領域で加工を開始することができる。当然ながら主軸や機械本体の熱変位が、主軸回転開始後ある程度の時間をもって収まり、その後長時間安定するというのが大前提であり、前述したμV1の主軸潤滑・冷却技術と機械本体の安定技術がこれを可能にしている。
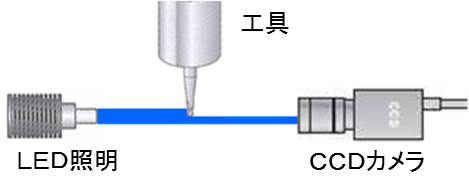
またワーク測定についても、直接CCDカメラでワークを測定することはできないが、ワーク測定用のタッチプローブを撮像式工具測定システムにて測定し、各箇所の熱変位などの誤差をキャンセルさせた上でワーク測定を行うことで、測定精度を格段に向上させることができる。
ワーク測定や工具測定時には、機械の主軸原点位置からテーブル間の距離、タッチプローブの長さ、工具測定装置の高さなどを用いてワーク高さや工具長を算出する。これらの寸法は機械製作時に測定あるいはセットした数値を固定値として用いるが、当然ながら機械設置環境や運転状況によって変化しうるものなので、実測定時に誤差が生じてしまう。例えばμV1の主軸原点位置からテーブル間の距離は450mmであるが、機械製作環境と機械設置環境とに2℃の温度差があった場合、単純計算で熱変位が11μm生じることになるが、この数値分が測定誤差に加わることになる。一般的にワーク測定用タッチプローブ単体の繰返し精度が数μmであるのに、結果としてのワーク測定の精度が数十μmとなってしまうのはこういったことに起因している。撮像式工具測定システムを用いたワーク測定方法により、これらの誤差をキャンセルさせ、タッチプローブ単体の繰返し精度レベルにワーク測定の精度を高めることができる。
加工事例
μV1によるφ10μmの工具を用いた加工を実施した。切削条件を表1に示す。
ワーク材質 | 真鍮(C2801P) |
---|---|
使用工具 | φ0.01mm スクエアエンドミル |
主軸回転速度 | 10,000min-1 |
軸送り速度 | 1mm/min |
切込み量 | 0.2μm |
表1 10μm溝加工の切削条件
φ10μmの工具となると非常に折損しやすいため、1回の切込み量を0.2μmと小さくする必要がある。このため、工具測定やワーク測定の誤差に数十μmを見込んでアプローチの距離を取ってしまうと、その位置から数百回も切込みを繰返し、実際にワークに接触するまでに数時間を要してしまうことになる。
撮像式工具測定システムにより、工具とワークの測定を実施することで、工具を折損させることなく、また無駄な切込み動作を極力抑えて加工することができた。実際に撮像式工具測定システムにてφ10μmの工具を測定した時の画像を図2に、ワークに10μmの溝を加工した例を図3に示す。
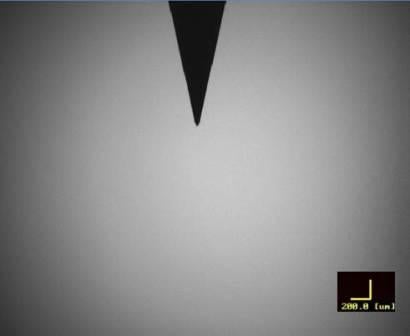
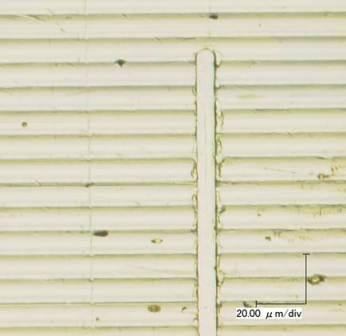
まとめ
小型精密加工機μV1そして「撮像式工具測定システム」を用いた微細・精密加工事例を紹介した。こうした微細な加工は、機械の性能のみならず、機上測定などの周辺アプリケーションが重要になる。今後も機械本体や周辺アプリケーションの更なる高度化を追求し、製造業の発展に少しでも貢献できるよう努める所存である。
※「型技術2011年7月号」掲載論文