Future Technologies
Second generation of E-Axle
Further development of the Heart of the EV
Compact, Light, and High-power Traction Motor
In 2019, Nidec became the world’s first company to successfully mass-produce E-Axle, a traction motor system for EVs. Our company offers a wide lineup of E-Axle, from 50kW – 240kW, to cover all segments of electric vehicles, ranging from compact cars to large SUVs. These traction motor systems are adopted by growing numbers in auto makers in China, the country advanced in introducing EVs, and other countries. These models are overwhelmingly more compact and lighter than gasoline engines of the same classes, while boasting high torques and output densities. The recently upgraded second-generation E-Axle units enjoy a torque and an output density 20% better, and a weight 19% lighter, than its first-generation predecessor, further enhancing its characteristics.
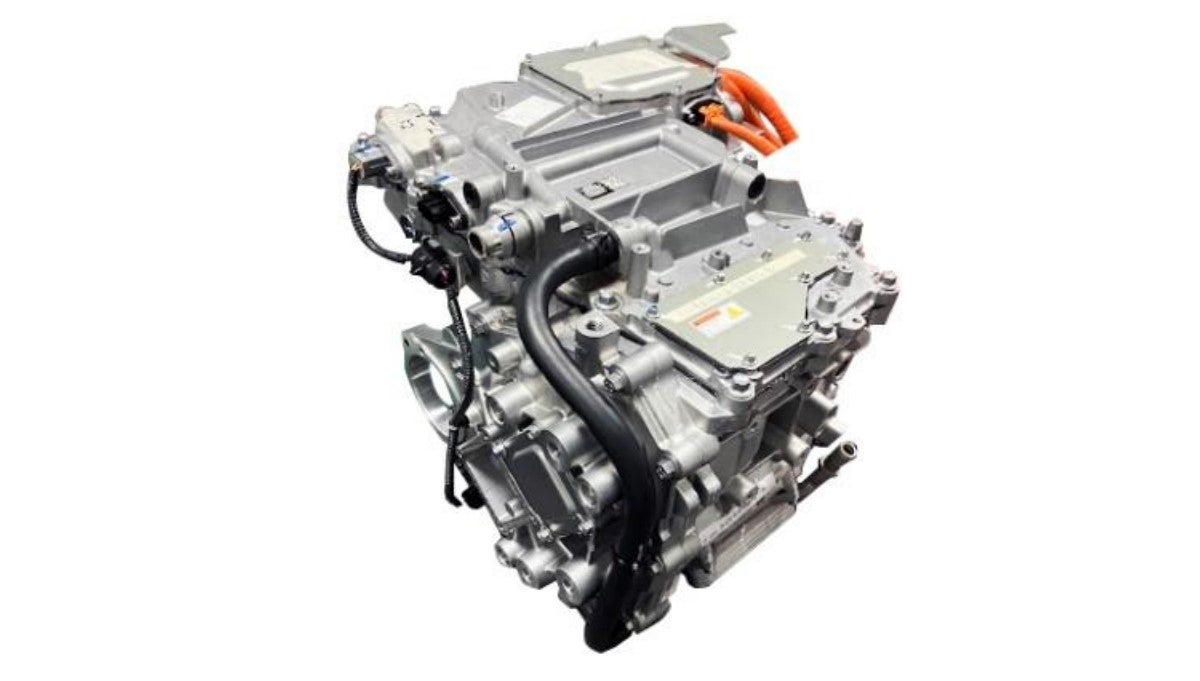
Densifying the Stator Core’s Winding Wires
Improving a motor’s efficiency requires densifying the winding wires of its stator, which is the source of torque (rotary power). Thus, for its first-generation models, Nidec developed a new method of inserting a cassette of winding wires for better density (the “cassette inserter” method), to achieve both a high production efficiency and an excellent slot-filling factor. Furthermore, for the second-generation models, Nidec revised the shapes of the stator cores to accommodate winding wires, and reduced the load of coils inserted into slots, while adopting the company’s unique wire-winding machines, to improve the coil share per slot section area by 10%.
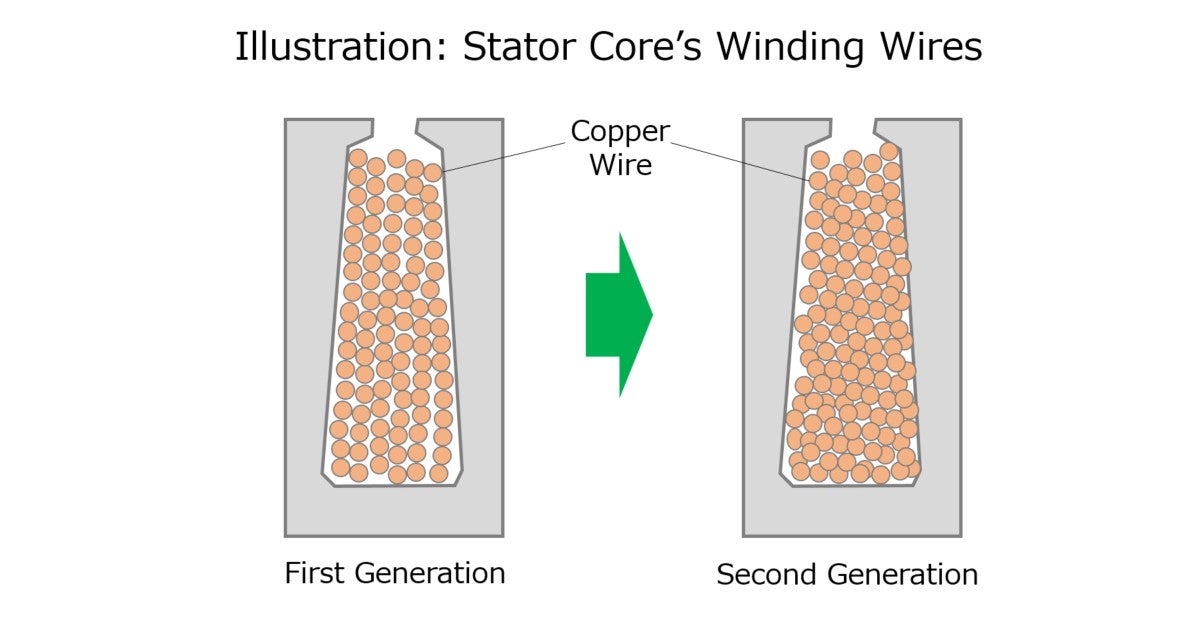
Significant Reduction of Heavy Rare Earth Usage
Heat-fighting measures are essential in improving motor efficiency. As heat affects the motor’s operating times and duration of time, the more output a motor generates, the more important its cooling unit becomes. In particular, a rotor’s permanent magnets, which generate electromagnetic force after interacting with a stator, exhibits a characteristic of its magnetic force weakening above a certain temperature. To counter this, for its first-generation products, Nidec would produce an oil-based cooling route on the inside and outside of each motor, to directly pour oil over a heated section to cool it, while, for permanent magnets, increasing the content of heavy rare earth to improve their thermos-tolerance. The latter, though, had a demerit of increasing product costs. This is why Nidec improved its cooling method for second-generation E-Axle units. We revised the cooling route inside the motor, and used a nozzle to spray oil cooled in an oil cooler to cool the stator from the outside. In addition, to improve the cooling performance further, we sprayed oil by using the rotor’s centrifugal force as well, to pour oil on the magnet, the rest of the rotor, and the stator coil. These actions enabled us to drive motors stably under a rated output even after employing a heavy rare earth-free magnet to a rotor.
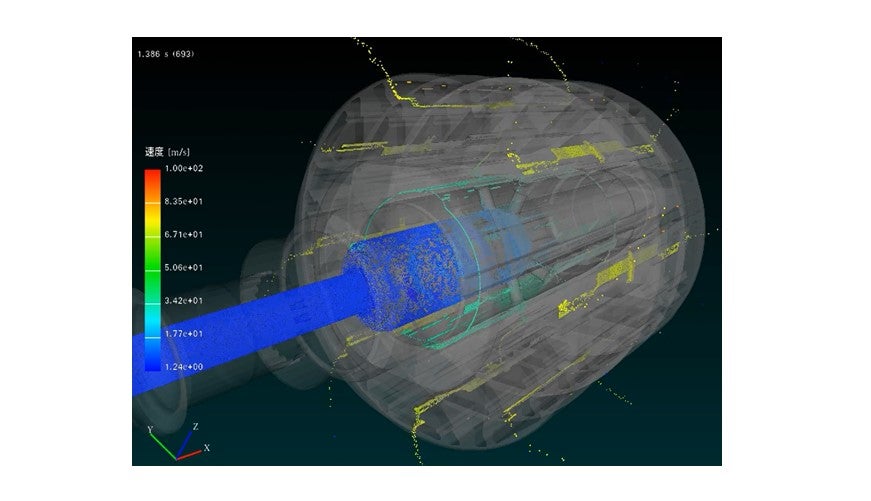
Making E-Axle Quieter
Since EVs are quieter than their gasoline-engine counterparts, noise from EVs stands out especially easily. Though Nidec’s first-generation E-Axle units achieved a high-level quiet performance, we continued with our experiment and analysis to pursue further improvement, to optimize the component layout, and adopted a newly designed gear, among other actions, to lead our second-generation E-Axle units to boast a noise level 9dB lower than that of its first-generation predecessors.
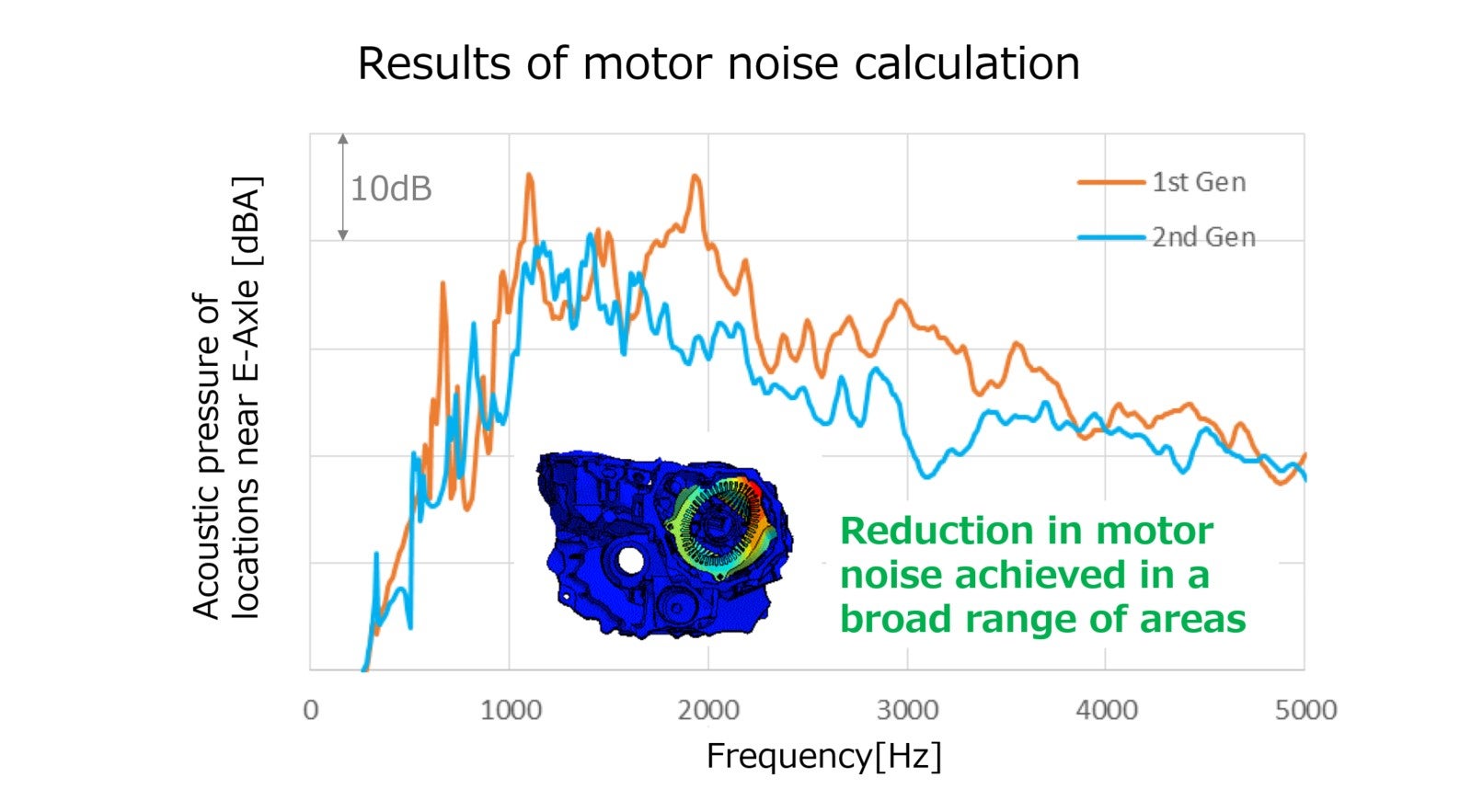
Constantly Contributing to the Evolution of the EV
2023 and thereafter, Nidec aims to replace the E-Axle units in the current lineup with second-generation products. Nidec stays committed to manufacturing products that contribute to the evolution of EVs’ performance and convenience.
Know More about E-Axle
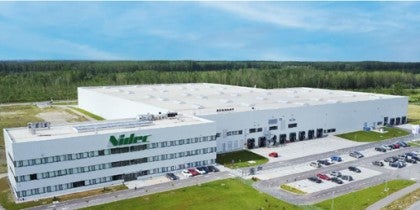
E-Axle: Its Strengths
Consistent system to handle everything from development to production
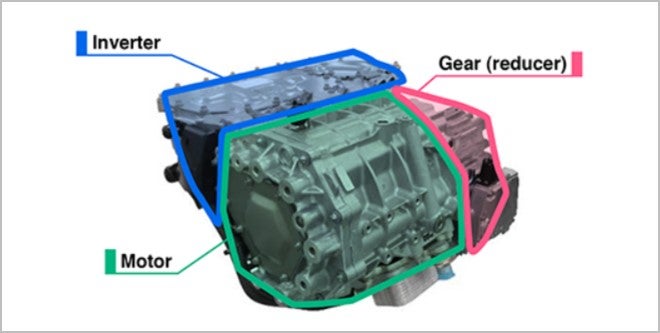
E-Axle, Nidec’s Traction Motor System
(EV Drive Motor System)
Nidec Became the World’s First Company to Mass-produce E-Axle, the Key to EVs’ Diffusion.