Nidec Engineers Taking on Challenges of Making Light, Thin, Short, and Small Products
Making short products
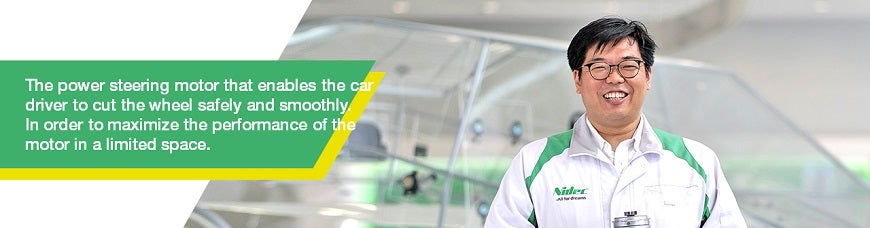
The root of the products is in its first generation.
The power steering system, which used to be hydraulic in many vehicles, is now replaced by the electric one, which has become mainstream as cars are growingly electrified. The power steering system (EPS) motor is now essential to automobiles. “Among automotive motors, making high-performance EPS motor is very difficult,” says Haga of Automotive Motor & Electronic Control Business Unit.
“An EPS has current of 100 - 150A running, and only with a Nidec motor does current run that high on 12V. On the other hand, even cogging torque, a torque pulsation that occurs when a motor is not energized with current, affects steering performance. When the driver moves a steering system, it is assisted by a motor, where current flows, but a minute pulsation causes a sense of discomfort to the driver. The torque caused by an EPS is approximately 4 - 8Nm, and we must keep cogging torque to 0.02Nm or less, and torque ripple to several percent or less. This all means that we must make motors that operate smoothly”.
Additionally, the motors, which are installed around the space-limited steering system area, must be compact as well. Nidec has been mass-producing its EPS units, ranging from its first generation, debuted in 2003, through the current fourth generation, and the sizes of these units have halved as they go down the generations.
“Each generation, we have reduced the size of the EPS units by approximately 10 - 20%. In particular, from the second generation, where the unit’s installation location was changed from inside the vehicle to its steering rack, it became important for us to reduce the unit’s length. Since the engine is placed on top of the ESP unit, and with exhaust pipe and other components placed nearby, we struggled to reduce our ESP unit’s size while accommodating the strict thermal environment.”
Haga, who has been designing the second generation of Nidec’s ESP units and after, says that his root is in the first-generation EPS unit’s unique design, which he saw as a newly hired employee.
“Back then, they let me assemble a prototype, but I first couldn’t understand how to wrap a copper wire to assemble the unit. I had to have senior employees help me to complete the process. I couldn’t even believe that the unit can be mass-produced without human labor. To mass-produce the unit, people adopted a special-shaped core, and remade jigs repeatedly. To this day, the process serves as my role model in using ideas to meet high-level demands. The design I saw back then was so unique that I still don’t think I can make such a design.”
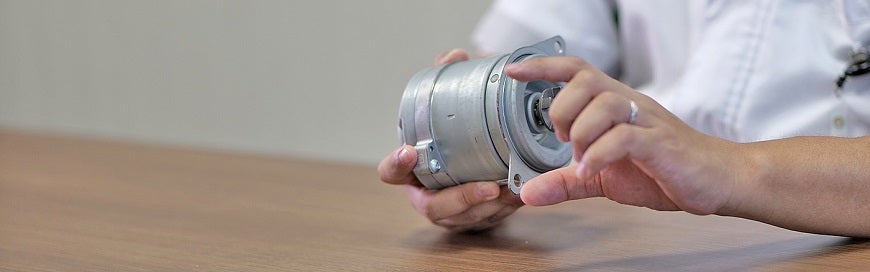
Becoming a market leader by developing an innovative product assembly method
As explained already, from the second generation and on, the EPS unit is placed right beneath the engine, requiring Nidec to accommodate the strict thermal environment. Until then, with the unit placed inside the vehicle, the heatproof temperature condition was 85ºC, but it was changed to 140ºC, which indicates how tough the heating environment has become.
“With the temperature rising that high, motors that would function at normal temperature will stop working properly due to demagnetization. This product prompted us to review magnet composition and orientation with magnet manufacturers, and re-study the principles of magnets. We probably had our magnet manufacturers try at least 10 different compositions.”
The EPS unit’s performance improved further with the production of its third generation, which was adopted for a platform that a major automotive equipment manufacturer was developing, making Nidec a market leader in the field of EPS.
“This product, whose design was kept as simple as possible, later became a standard EPS. We had to change its design five times or so. As platforms were created, this product can accommodate both right and left steering wheels. Cogging torque is kept extremely low as well. Though it is possible to reduce it by controlling it now, the control technology wasn’t as developed as it is today back then, and we would use the motor’s main unit to reduce cogging torque.”
Most important is that Nidec developed its mass-production technology while developing the product, to realize an innovative mass-production method.
“Though we cannot disclose details, I can say that we were able to mass-produce our motor by employing ideas from its first generation. Without this technology, this latest product might not be in the market now. We were happy to be told directly by a major automotive equipment manufacturer’s person in charge that they were able to make a wonderful products thanks to our EPS units. To this day, I still think that this is an innovative product that serves as a turning point for Nidec’s EPS business.”
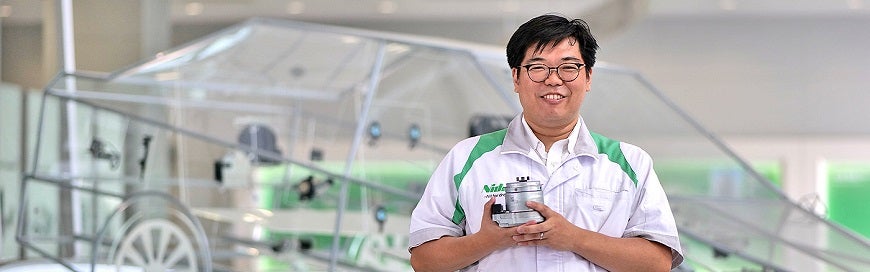
The technology of bending with a motor remains unchanged, regardless of the product’s shape
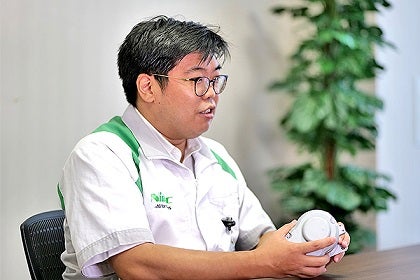
From the fourth generation on, the required durability performance became significantly tougher: Until then, the EPS unit would have to be maintenance-free for 100,000km for 10 years, but the durable years were extended to 15 years or even 30 years.
“We are now required to ensure that the EPS unit works properly even when a vehicle is submerged in water, or when water enters the unit after the steering shaft’s boot breaks. This indicates that our customers now assume that their vehicles will probably be used in such harsh environments.
Though our EPS units may look alike generation after generation, the newer unit has the motor-accommodating section, which, in the third generation, was a split-type, o-shaped ring to resist water, was made into a cup-like shape to make a waterproof structure. In addition, we reduced the unit’s size by approximately 20%.”
In the next, fifth generation, with limits in making only the motor small to make a smaller unit, Nidec plans to reduce the EPS unit’s size by making a power pack containing a motor and other parts such as the ECU, a unit for our motor to control. Furthermore, eyeing the age of autonomous driving, we will examine the future of the steering mechanism.
“Unlike in the current age, where the EPS unit simply assists people’s power, we will be required, in the age of autonomous driving, to improve our unit’s output to move the steering system only with a motor. As vehicle electrification progresses, one may be able to change a car’s direction by controlling in-wheel motors instead of using the rack system in use now. Still, however, the car-curving technology will remain essential, and motors will be definitely needed for the technology. This means that there is room for motor engineers to be able to contribute.”
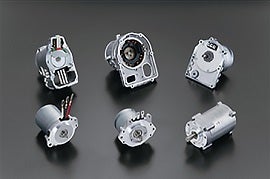
Power Steering Motors (1st – 3rd Generations)
Nidec strived for the reduction of cogging torque, which is the largest challenge affecting pure electric power steering systems. Nidec overcame multiple problems one after another by applying accumulated technologies and creativity to develop solutions.
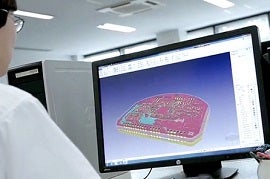
Integrated Electric Power Steering Motors and ECUs
The Smallest and Lightest Class of Power Packs in the World
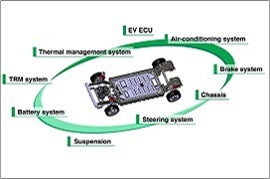
EV platform
Nidec embarks on the development of a versatile wheeled platform – the crucial element to dissemination of EVs.