Implemented Solutions
Super-flat Actuator FLEXWAVE with Axial Flux Motor
- NEEDS
- Supply power assist suits appropriate for nursing care fields.

- SOLUTION
- Develop a flat, high-power-density actuator.
Utilize shape-related merits to a reducer-equipped, light, thin, short, and compact actuator.
Japan’s elderly population keeps increasing, and is expected to reach 30% of the country’s entire population in 2025. Japanese nursing care facilities are already suffering from a serious labor shortage, and easing nursing care personnel’s burden is a social issue. It is amid these circumstances that the needs for power assist suits, a tool to support physical functions, are on the rise. Their market will soon reach 12 billion yen, and some are estimating it to more than quintuple in the next five years.
Actuators to drive joints are essential components for power assist suits. Each actuator comprises a reducer, a controlling unit, and a motor, a source of driving force. Together, they generate a strong force as the person wearing a power assist suit moves, relieving burden from the waste and feet.
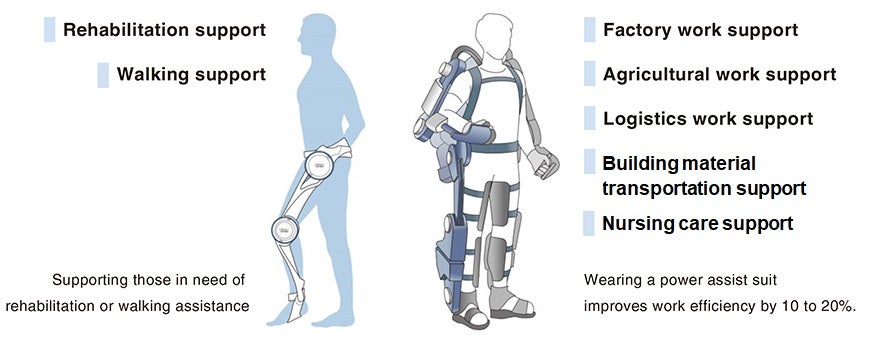
Using a “shape-changing gear structure” to realize seamless control and a thin actuator
In principle, any drive component’s actuator has to be large and thick as it is required to generate large power. However, at medical care fields, where personnel need to be able to walk narrow passages and walk through narrow door spaces, sufficient caution must be taken to keep actuators’ users from being injured. This is why power assist suits’ actuators are required to be thin and compact.
FLEXWAVE, a reducer that NIDEC DRIVE TECHNOLOGY started supplying in 2015, is thin enough to meet such requests from nursing care fields. Even the middle-type, which is for the waste, is only 20mm thick, while the diameter is 90mm. Additionally, to realize nursing care personnel’s movements accurately, the actuator must be controlled extremely accurately. Meeting this requirement means to address the issue of backlash, which is created between gears. FLEXWAVE, whose externally toothed gear is combined with an internally toothed one, has inside an elastic bearing, whose shape changes ellipsoidally. Furthermore, the externally toothed gear, which is made of a highly ductile, thin steel-type material, is deformed with the bearing to mesh properly with the internally toothed gear, making FLEXWAVE’s backlash low. With its gear ratio freer than before, FLEXWAVE boasts a significantly seamless control of 50 – 120.
Combined with a new-type motor to make a thin, high-power-density product
Another product, the axial flat motor (AFM), is a device that Nidec Research and Development Center, Taiwan developed for super-flat actuators, and it has a structure that is gaining attention recently. While general radial flux motors (RFMs) are of a vertically long shape to secure sufficient torque, the AFM secures torque with its long diameter.
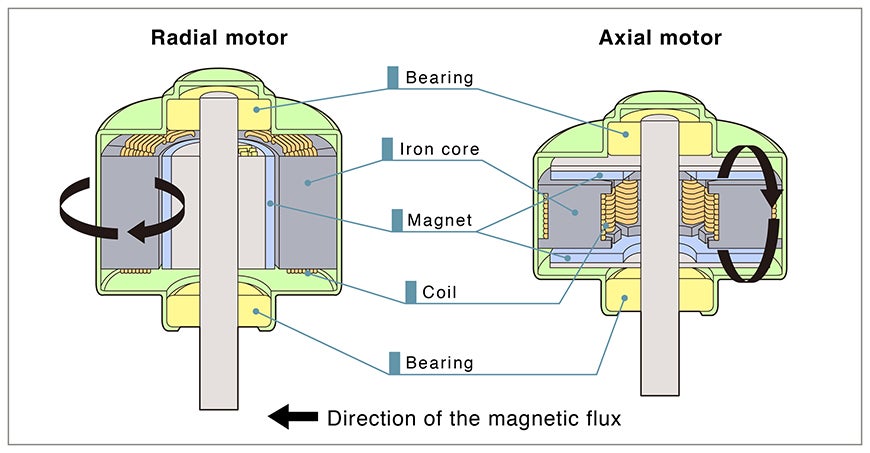
This is why the AFM is only approximately 21mm thick, despite its high output of 170W.
Taking advantage of synergies in the Nidec Group, NIDEC DRIVE TECHNOLOGY planned to make an actuator that would combine FLEXWAVE with an AFM, and successfully developed super-flat (41.5mm thick for the aforementioned model with a 90mm diameter) and light actuators. With three models with different outputs and size, the actuators are used for a wide range of power assist suits’ applications, based on where on the body the actuators are used and the nature of work.
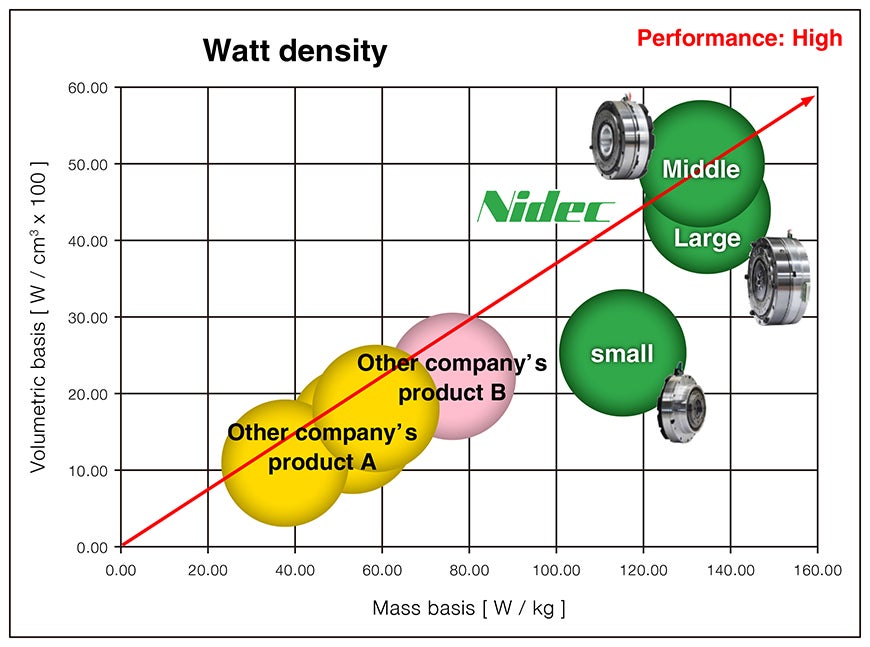
Discussions are underway at present on using the actuators in the field of personal mobility, including electric wheelchairs, in addition to power assist suits. The actuators can be used for SCARA (selective compliance assembly robot arm) robots and other production equipment, and autonomous-mobile, multi-joint robots as well. Days will come for us to live with robots in the city and home in a not-so-distant future. The needs for compact and high-output actuators will increase rapidly. It is to meet those needs that the Nidec Group will further accelerate the pace of its research and development.