Implemented Solutions
F5B Electric Glider Competition
Nidec is challenging the limits of compact, high output, and high efficiency motors in the world's premier motor glider competition.
Global warming and fossil fuel depletion.. The automobile industry is rapidly changing, and moves toward manufacture of electric-powered equipment are accelerating. Subsequently, motor and peripheral device technologies are becoming increasingly important. Automobile motors, used in conditions in which there are large load variations and limited space, are required to be compact, have large output, be highly efficient, have a wide range of variable speed operations, low noise, a wide operating temperature range, and other features.
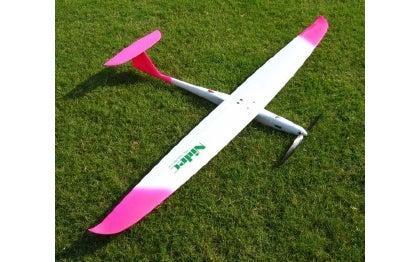
The automotive motor, in particular the traction motor, is the target domain that is important to Nidec. The target that was selected to enable Nidec to efficiently learn and acquire knowledge about traction motors and peripheral device technologies is the F5B electric glider competition. F5B is also known as the F-1 of radio-controlled airplanes. A high-output, compact and lightweight motor is essential for accelerating the airplane to a vertical climbing speed near 200 km/h. In order to play an active part in the tournament such as the World Championship, and to aspire to achieve a top world ranking, we need to not only develop a high-performance motor but also to have complete power to develop and operate the system including components such as the ECU, batteries, data logger and other peripherals.
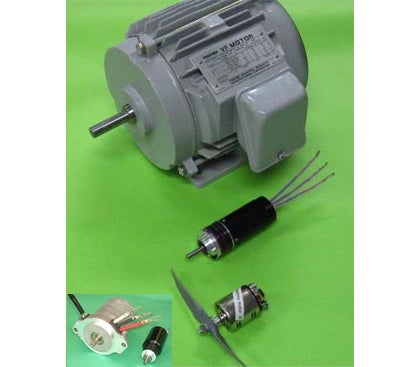
The Nidec's motor for the F5B finally achieved the specs of 19.5-V (average) input voltage, 300-A maximum current, and 2.4-kW maximum output at 84,000 rpm. The speed of fan motors used for the server requiring high rotation speed is at most 20,000 rpm. The speed of our motor is very high, and the rotor magnet was scattered by the centrifugal force in the early stages of motor development. As the external dimensions are 39 mm diameter x 110 mm length x weight 300g, the power-to-weight ratio of our motor is 8 kW per kg. This performance is much higher than the 6 kW per kg of an F-1 racing engine. As the motor is driven by low voltage and large current, both temperature and electromagnetic fields increase to high levels inside the motor. We thought that a semiconductor sensor would be difficult to install, so and we used sensorless control. Due to the space, we could only use a small-package microprocessor, and we studied how to install the control algorithm software in a compact space because the small microprocessor has limited processing capability. We had to solve various problems including overall hardware and software design.
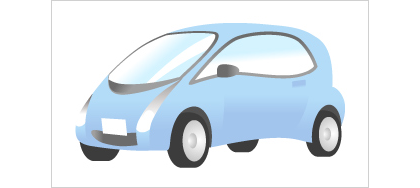
This project was launched in 2005, the prototype was completed in 2006, we won the Japan championship when we participated in it for the first time in 2007, and we captured the world championship title in 2010. Our F5B motor project was very successful. The F5B motor, that achieved best-in-the-world status, has the same performance as automobile motors in the areas of low voltage, large current, compact size, and battery driving. The ECU that we developed in parallel can also be used for automobile applications in ways that maintain performance in high temperature environments, have sensorless control to reduce wiring requirements, and superior speed control. Taking advantage of skills and experience gained from the F5B motor, we will further refine the gearless driving and sensorless control technologies in future. In addition, we will build a technology platform for high-current and high-output motor design, and strive to deploy limited design technology in the automobile and aerospace industries.