Implemented Solutions
Integrated Electric Power Steering Motors and ECUs
The Smallest and Lightest Class of Power Packs in the World
Electric power steering motors—originally developed with reduced energy consumption in mind—are about to take another evolutionary leap. Responding to the need for more compact and lightweight automobile components, we have integrated our motors and electronic control units, resulting in a more space-efficient product. Furthermore, combining these previously separate components comes with a host of other benefits, including reduced manufacturing costs due to cutting down on assembly time. In addition, integrated motors and ECUs also eliminate the need for a connective medium, bypassing the problem of noise introduced by the wire harness acting as an antenna.
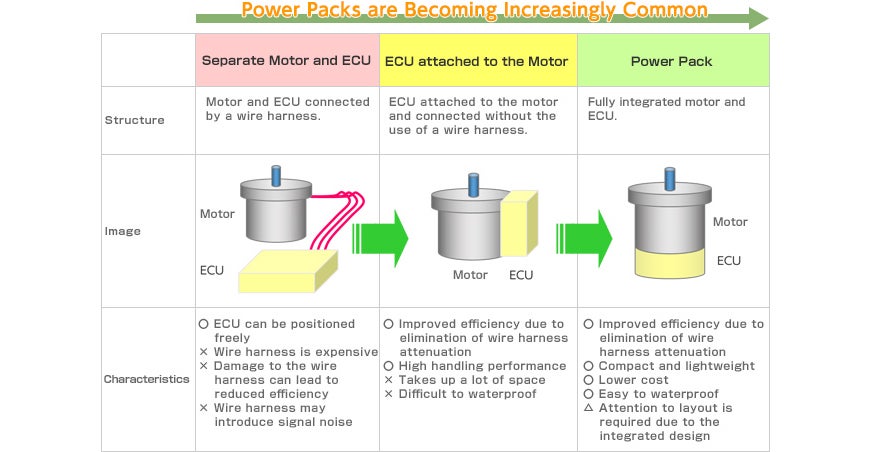
Completely integrating two separate products does not come without technical difficulties. The first issue that presented itself was how to deal with the combined problem of heat generated by the motor and the lack of a way for that heat to escape due to the integrated structure. This problem was further complicated by the reduced heat dissipation capability of the ECU's integrated circuits that need to be miniaturized together with the motor. The relatively large electrolytic capacitors, in particular, are negatively affected by heat and run the risk of drying up as the heat causes the electrolyte solutions to evaporate. Furthermore, solder joints, as well, are heavily affected by heat and may experience thermal fatigue leading to the appearance of internal microscopic cracks.
In order to overcome these problems, we have adopted the latest generation of compact low-impedance capacitors, allowing us to develop a layout that solves the heat issues by miniaturizing the other components—all while retaining high operational reliability. The solder-relate issues were overcome with composite materials and improvements to the shape of the solder lands.
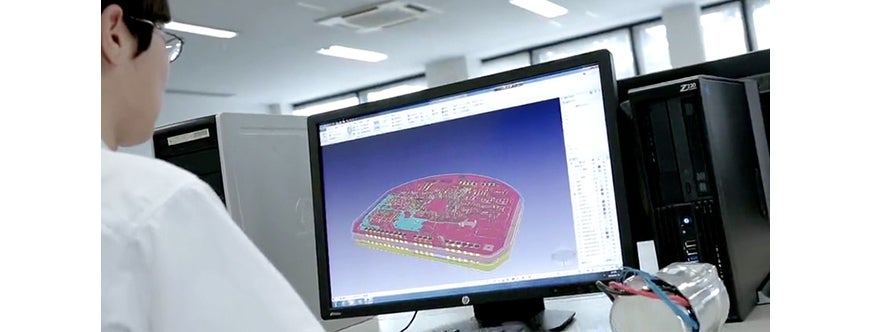
Reduced size and weight is not the only benefit of our integrated motor/ECU power packs; we have also taken great care to improve their controllability as well. In order to improve steering feel and reduce noise and vibration, we have developed control methods that ensure that the steering assist torque produced by the motor is applied as smoothly and naturally as possible by minimizing cogging torque and torque ripple. Our first step was to gather data by equipping an actual automobile with one of our electronic power steering power packs and repeating basic maneuvers. Next, we explored the relation between the torque supplied by the EPS power pack and the steering feel and designed a set of suitable control logic algorithms. This process was then repeated several times in order to further refine the control logic. As a result, we succeeded in creating an integrated EPS power pack that is not only compact, but also capable of minimizing torque ripple and contributing to a natural steering feel with minimal noise and vibration.
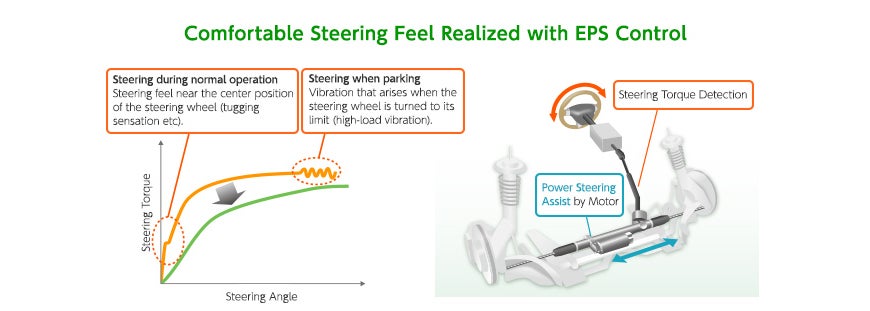
Developer's Comment
During the development of this product, we also had to overcome a number of other hurdles, such as issues related to the MR sensors used in place of conventional resolvers etc. Next, we would like to focus on support for autonomous driving. Fault-tolerance in case of breakdowns, seamless switching between human driving and computer driving—there are numerous problems left to be solved before widespread autonomous driving can become reality. However, innovation in this field is unlikely to slow down and our mission is to develop new products that reflect the latest trends in technology. We have already taken the steps from stand-alone components to modules and our electronic control capabilities have evolved from module level to system level. The challenges ahead of us are becoming increasingly more advanced. Looking forward, we strive to continue improving our technology in order to maintain our reputation as a reliable partner.