Implemented Solutions
Deep sea AC motors for submarine cable burying ROVs
Motors that can withstand the pressure of ocean depths of 4000m
developed for submarine cable burying ROVs
- NEEDS
- Precise operation and resistance to water pressure 4000m below the ocean's surface

- SOLUTION
- Precise operation and resistance to water pressure 4000m below the ocean's surface
One of a kind motors indispensable for laying communications cables in the seas around the world
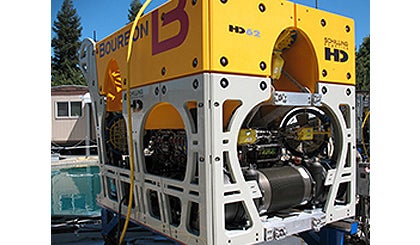
Submarine cables have been laid in the seas around the world since 1850 when the first cable was deployed between Dover (Great Britain) and Calais (France) in 1850. Due to their high capacity and signal quality, these cables have remained the principal method of transmission of information even after the development of wireless transmission and the appearance of satellite communication. Placing a submarine cable on the floor of the sea requires the use of a dedicated cable layer ship together with a remotely operated vehicle that digs through the seabed while burying the cable so that it doesn't get swept away by the ocean currents. Nidec KINETEK develops and manufactures the squirrel-cage induction deep sea AC motors used for these ROVs.
These deep sea AC motors use a special construction and are filled with incompressible oil to be able to withstand the pressure of ocean depths up to 4000m below the surface.
Functionality and performance guaranteed by advanced manufacturing and testing methods
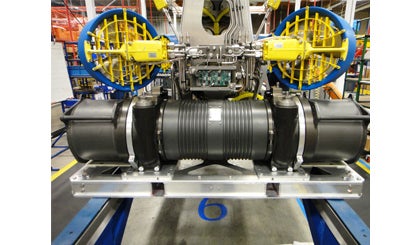
Since the interior of the motors is filled with oil, some friction is added to the system, lowering the RPM of the rotor. To counteract this friction, special attention is paid to the design of the rotor shape.
Moreover, a number of special techniques are employed in the manufacturing process as well. For example, the stators are manufactured by centrifugal casting to ensure a fine structure free of casting defects such as gas porosity. Furthermore, a vacuum and pressure impregnation process is used for the stators to avoid void formation. Before the motors are shipped, they are subjected to an array of thorough tests including thermal resistance tests, over-voltage and under-voltage tests, testing of torque, RPM, current, voltage under brake loads and leak-down tests. These tests are carried out in a water tank to simulate the cooling effect of sea water on the motor and all of the data is recorded by computers allowing for detailed analysis. This thoroughness is reflected in our quality assurance system as well, guaranteeing reliable operation at ocean depths of 4000m.