NIDEC's Technical Capabilities
Transfer robots that enable an optimum wafer transfer in a vacuum environment
Securing, even in a vacuum, a degree of freedom equivalent to that in the air
n the manufacturing process of liquid crystal panels, organic ELs, and other displays where production cost must be reduced while screen sizes must be made larger, increase in the sizes of mother glass substrates and in the processing speed is constantly required. Recent years, when price competition has intensified, have witnessed a further increase in the sizes of the mother glass, even to 3m x 3m in some cases. The Nidec Group provides large-display transfer robots for vacuum manufacturing processes.
The mother glass substrate’s thin-film, vapor deposition, and other processes must be performed in a vacuum environment, as they require an extremely high level of cleanliness. Robots that operate in a vacuum must have a built-in seal in their joints not to release the air, dust, etc. from the inside of an arm or other parts. Seals, which impede a robot’s movements, tend to restrict the range of its joint motion; however, Nidec’s vacuum transfer robots has a degree of freedom equivalent to that in the air.
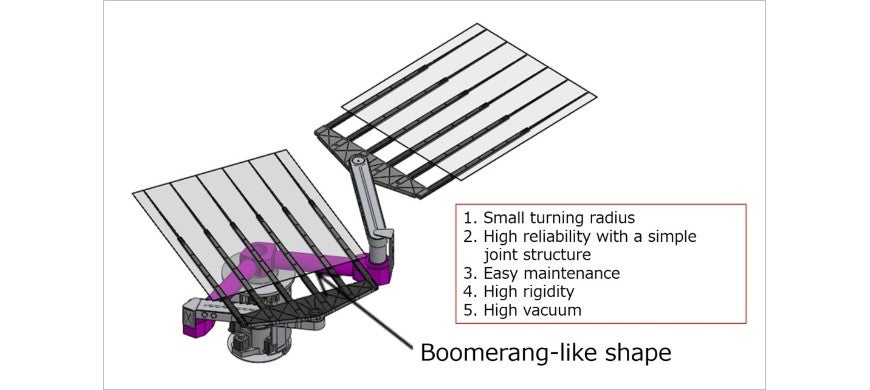
The Nidec Group boasts two types of vacuum transfer robots: boomerang and scalar. The former has the merit of a small turning radius. In addition, with the number of dust-generating joints held to a minimum, the cleanliness in a vacuum is kept sufficiently high.
Using reducer-integrating seals to generate a vacuum
The boomerang-type mechanism has been used for, among others, wafer transfer robots in a semiconductor manufacturing process. However, displays’ mother glass substrates, much larger than semiconductors’ silicon wafers, had to be made at least 10 times larger than them, in which process securing rigidity is a major issue. The conventional way to do has been to use a belt, etc. to convey the motor-generated driving force, but it has been difficult to produce a large and highly rigid display, as this method requires a complex structure.
Thus is why Nidec applied a motor and a reducer in each joint of the robots, while adopting reducer-integrating magnetic seals, a critical component for robots to work in a vacuum, to keep the seals’ number to a minimum. Using fewer seals means a better rigidity and a higher degree of freedom for movement. The Nidec Group achieved a vacuum by using fewer sections that must be shut off from contact with the outside.
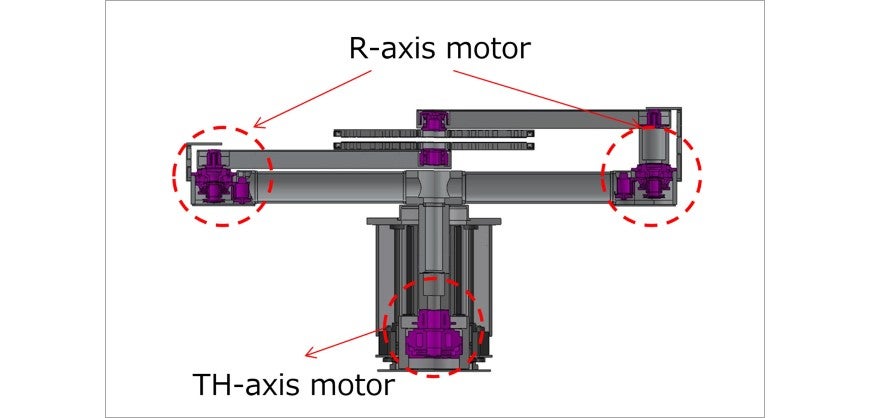
Nonetheless, temperature management is a major issue, as reducers tend to become hot. Nidec’s vacuum robots circulate the air inside their arms to manage all temperatures. With each joint having a different calorific value from another, we install a radiating heat sink based on each such value, or adjust the airflow, to keep the reducer’s internal temperature constant.
The scalar-type robots used in an organic EL manufacturing process has the merit of arms with a high degree of freedom. Despite the small number of joints, the robots can insert panels into, and remove them from, two vapor deposition machines in a juxtaposed position, contributing significantly to improving the entire process’s efficiency.
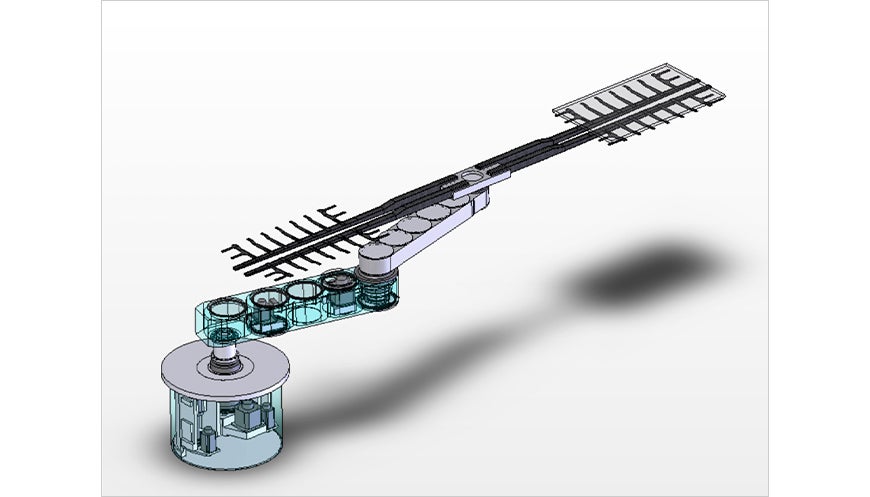
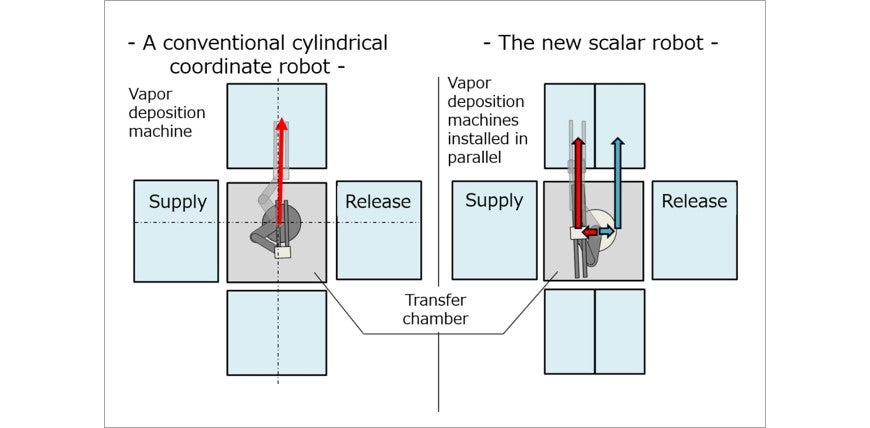
In this section, too, we use the aforementioned reducer-integrating magnetic seals to enable the robots to move more flexibly, while achieving high rigidity and vacuum for them. In addition, the use of the units for the boomerang-type robots keeps cost low.
Adopting mechanisms and designs based on motors’ and reducers’ features, Nidec offers solutions such as robots with performance capability required in a manufacturing process.