NIDEC's Technical Capabilities
The Servo Technology of the Future
Completely New Servo Technology with Support for Control Systems of Unprecedented Scale and Precision
The rise of factory automation has brought many benefits to manufacturing. Machining, in-factory transportation, assembly—every step of the manufacturing process is evolving in parallel with advances in automation technology. In the midst of this trend, control technology—the core of automation—has seen remarkable development as well. However, as the requirements on the servomechanisms controlling robots and other automated equipment continue to increase, current control technology is unable to keep up and the need for a new groundbreaking solution has emerged.
Until now, a control loop feedback algorithm referred to as PID (Proportional-Integral-Derivative) control has been the main tool used to control the movements of robots and other equipment. PID control works by calculating the difference between a desired numerical value and the actual value of the controlled object based on the three terms P (Proportional), I (Integral) and D (Derivative) and then attempting to minimize this difference through a feedback process. These systems are designed without going through meticulous testing of the controlled objects and instead rely on continuously adjusting the control parameters by trial and error. Due to being an analog/hardware control method, it is free from responsiveness-related problems, contributing to its use in a number of separate fields for a wide range of applications including aircraft autopilot systems, motors and hydraulic systems. In this way, PID control has evolved to take on many different shapes. However, as the individual control systems grow in scale and require increasingly higher precision, the number of controllers necessary increases as well, making the trial and error process considerably slower. Moreover, there are even cases where PID control fails to achieve the required performance altogether.
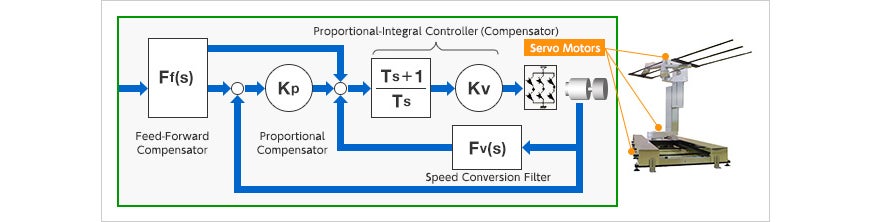
One of the fields in which PID control is unable to keep up is that of industrial robots. NIDEC INSTRUMENTS develops and manufactures a wide array of industrial robots for a variety of applications, including robots used to handle glass substrates for LCD panels—an application which has seen remarkable development recently. As end-products get increasingly larger and focus shifts to manufacturing efficiency, the size of the mother glass, the substrate that is cut into individual LCD panels, increases year by year—the latest models can be as large as 5.5 square meters. In order for the robots to be able to handle these incredibly large and thin mother glass substrates, their movements need to be controlled with minute precision as the slightest mistake runs the risk of breaking the glass. Moreover, the increased size of these industrial robots introduces a number of other problems; they become more susceptible to resonance due to lower mechanical resonance points and experience great variation in burden depending on the load carried by the robot and the rate of extension of its telescopic arms. Even in the face of these issues, faster and more precise operation is absolutely essential due to the demand for higher productivity.
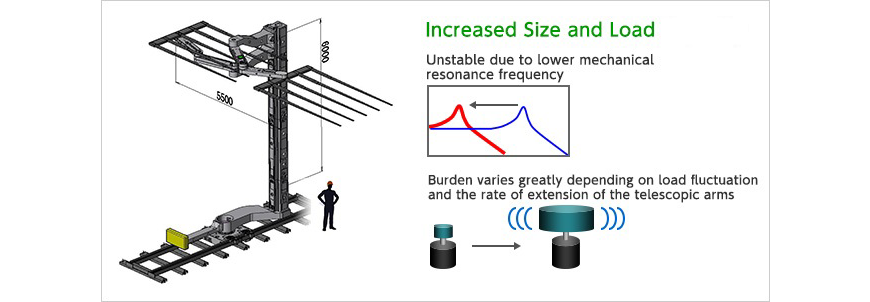
High-speed/high-precision operation of large industrial robots necessitates properties such as:
- Closed-loop characteristics accommodating lower mechanical resonance frequencies
- Disturbance-response characteristics allowing for robust and stable operation by compensating for significant load fluctuations and disturbance
- Command-response characteristics that enable improvements in efficiency
Large industrial robots operating with high precision at high speeds require a control method capable of isolating the—at a first glance mutually exclusive—properties above and controlling them separately. As parameter based control systems such as PID control are incapable of this, the engineers at NIDEC INSTRUMENTS had to develop an entirely new control method based on current control theory, in which the controlled objects are expressed as mathematical models and paired with suitable algorithms specifically designed for each individual object. Moreover, by abandoning the idea of an overall detailed model in favor of using a rough model coupled with a disturbance observer function—ensuring robustness in designated local bandwidths by compensating for uncertainty and variation—we succeeded in devising a versatile yet stable control method. Additionally, we designed the system so that the closed-loop characteristics can be freely matched with the mechanical properties of any chosen model. Finally we also improved the command-response characteristics of the feed-forward controller while also allowing them to be configured freely by applying feed-forward compensation based on the closed-loop properties of the matched model.
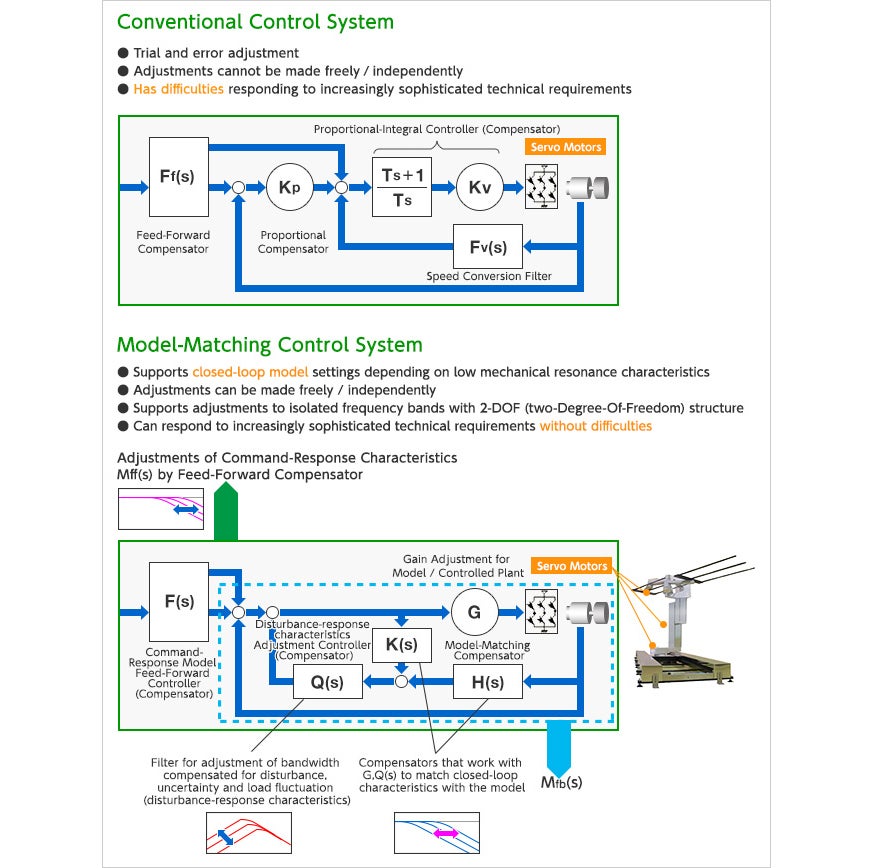