NIDEC's Technical Capabilities
Semiconductor wafer transfer robot
Using the revolutionary 3-link arm to reduce space
It is safe to say that semiconductors are a foundation of industry, supporting many things from smartphones, PCs, autos, and other products people use daily to communications networks and other parts of social infrastructure. Semiconductors require a long and diverse manufacturing process, and an extremely high level of cleanliness. The Nidec Group manufactures robots to transfer wafers to semiconductor production sites.
The robots receive round wafers from the previous process of production, and transfer them to the next part. Recent years have witnessed a rise in demand for compact semiconductors to save the size of space to be kept clean, and install more semiconductor manufacturing equipment in limited space.
Ultra-clean semiconductor transfer robots that Nidec Group developed
The “SR8241” series robots use three arms based on the Nidec-unique 3-link mechanism. Unlike the two-link, two-arm system that other companies use, the three-arm system keeps each arm short, making the machines’ operating range 72mm shorter. This improvement has made a significant impact on the world of semiconductor manufacturing equipment, where it is required to be made smaller by the unit of 10mm.
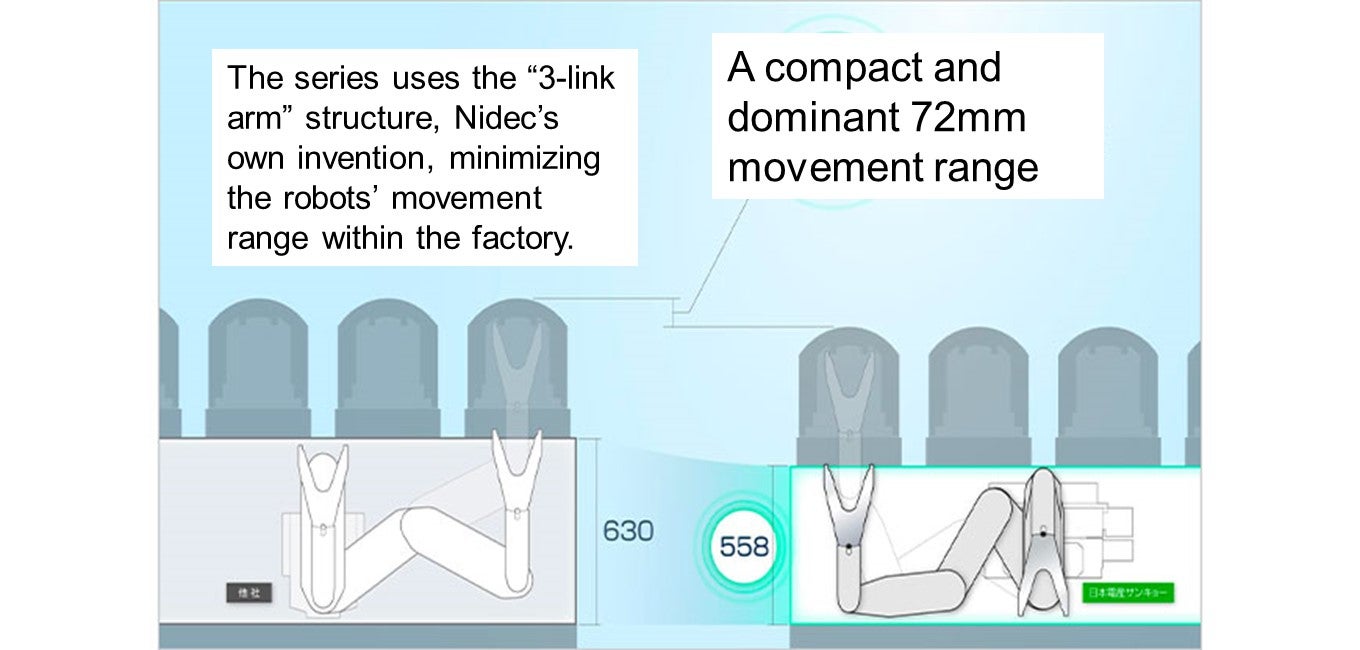
A transfer robot move back and forth between four cassettes placed in the front and the rear sections respectively. Narrowing the robot’s movement range enables you to need compact semiconductor manufacturing equipment. In addition, with the use of longer arms, the three arms will be able to handle cassettes even if more of them are used in the future.
The robot’s movable link is controlled by a motor. The SR8241 series controls more links than its predecessors did, but the number of motors to use remains unchanged from its two-arm counterpart, minimizing cost increase.
The cleanliness technology that underpins the 3-link mechanism
Microscopic particles that are the size of 0.1 micron or so cause serious contamination in a semiconductor manufacturing site. Semiconductors are produced in a clean room to avoid such contamination, but particles are generated from their manufacturing equipment itself, especially its robots’ moving sections, which have bearings and oil seal where metal and rubber grind against each other.
Nidec successfully adopted more links to its semiconductor manufacturing equipment’s arms, where particles are generated, by using its technology to keep them from being released into clean air. This is all possible with a Nidec-unique seal structure on the robots’ joints to prevent the release of particles.
The robots have an exhaust fan at their bottoms. A downward airflow is generated inside each robot, releasing particles to under the floor. Particles are generated in the wafer guide’s movable section as well, but the vacuum-creating particle-capturing mechanism inside the robots keeps the space clean. These technologies enabled the SR8241 series to obtain the highest Class 1 cleanliness certificate in the ISO’s clean room class categorization.
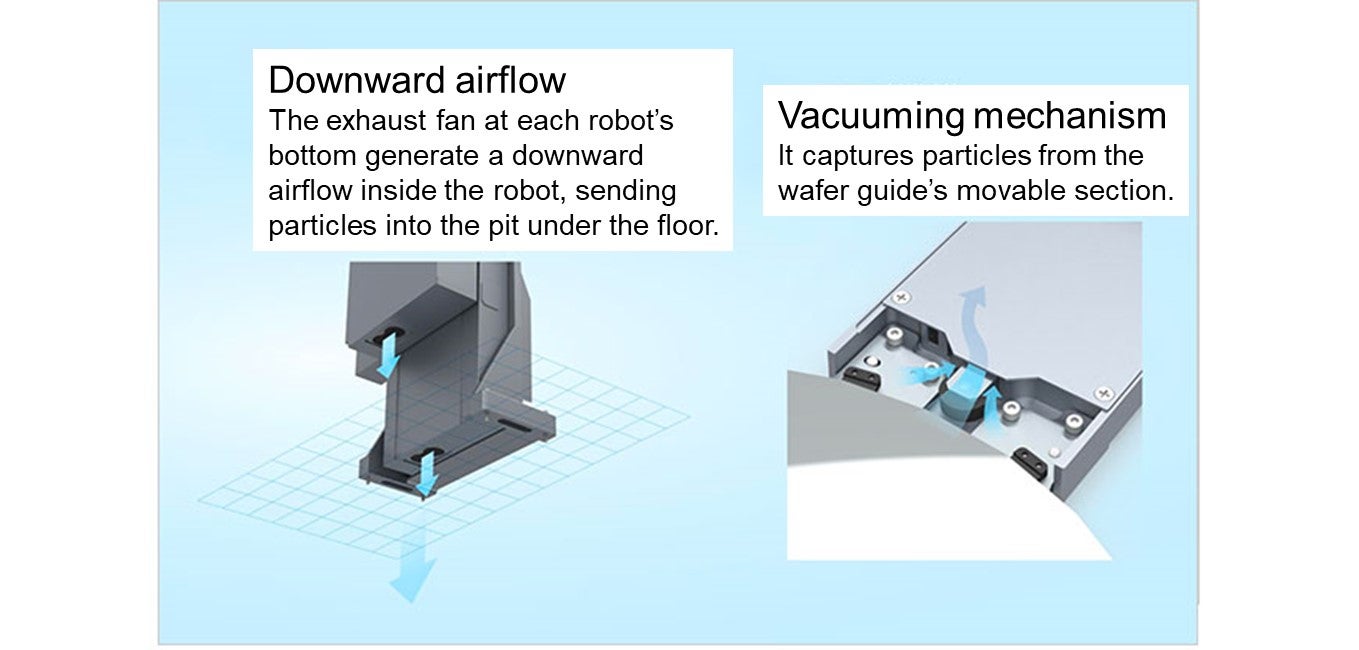
These cleanliness-related technologies enabled a mechanism that keeps particles from being released from a robot’s movable section, leading us to adopt the 3-link mechanism with more movable sections.
Simple movements to achieve high durability
Though the number of links has increased to three, each link’s movement is kept small, with each arm’s movements made simple. This is why the load on to the movable section has been reduced, leading us to secure an excellent durability in the robots. Though we recommend an overhaul of the robots every five years, the mean time between failures (MTBF, an index to show a machine’s reliability) of the SR8241 series has been verified to be longer than the period.
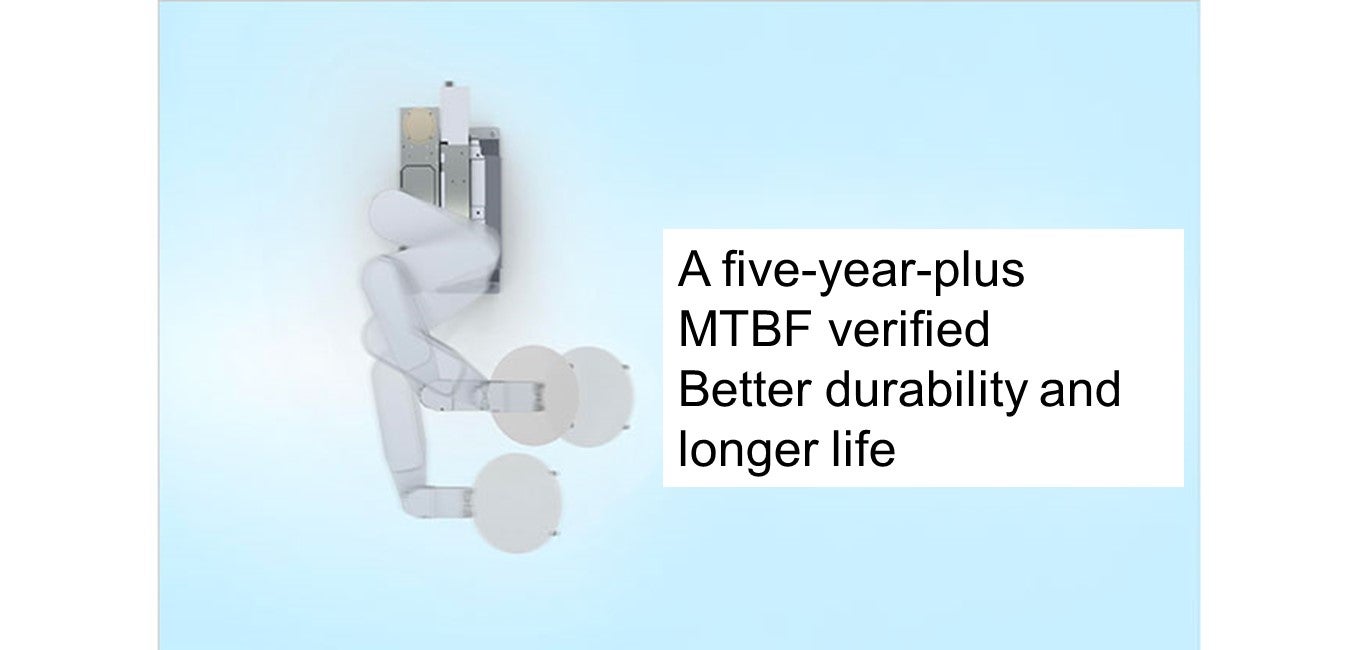
Collaborative ties among group companies has made possible both a speedy procurement of motors, which are key components of our products, and an overall well-balanced designing. The high reliability that the Nidec Group enjoys is, in a way, underpinned by its teamwork.