NIDEC's Technical Capabilities
Traction Drive’s Noise Reduction Technology
Realizing automatic guided vehicles for silence-required places
As Japan’s labor population decreases amid a dwindling birthrate and an aging population, a growing number of automated transportation vehicles are replacing humans to convey goods at logistics sites. Some of these machines are advanced enough not to have to use guiding tools like magnetic tape, and are expected to be utilized outside factories and warehouses. However, to be able to carry customers’ luggage at a hotel, moving documents and equipment in an office, transporting books at a library, etc., the vehicles need to be made quieter than they are normally required to be, for facility customers and users. This is why attention is being paid on the traction drive, a product that operates quietly.
Solidify lubricant oil with high pressure to transmit power

The traction drive is a technology that uses rollers, pressed against each other via a lubricant oil film, that roll together, as one roller conveys power to the other. The pressure on each roller’s contact section becomes very high. Liquid molecules move freely under normal pressure, but they line up regularly under high pressure, and become solid crystals. The traction drive uses this nature of molecules to convey power from a roller to the other.
Unlike gears, traction drives, which are not prone to impact noise caused by gears’ meshing force, are highly quiet, and can reduce backlash significantly, with rollers constantly contacting each other even when the drive is not rotating.
With no high-frequency speed fluctuation caused by gear teeth’s pitch errors (processing accuracy), traction drives can convey power very smoothly.
Since 1952, NIDEC DRIVE TECHNOLOGY has been producing traction drive-based industrial transmissions, which have been used for many industrial equipment so far.
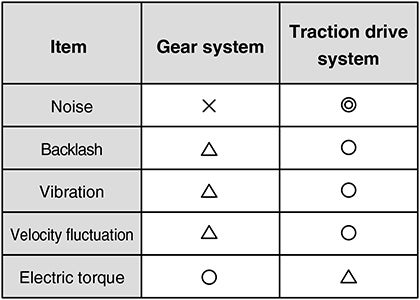
Miniaturization after repeated improvements
The traction drive has a demerit: Its transmission torque that can be realized at a specific size is smaller than that of the gear reducer, because of which the drive needs to be large in size. In the past, to achieve the same amount of torque, a traction drive of certain specifications would have to be four to five times the size of a gear reducer.
NIDEC DRIVE TECHNOLOGY has been trying to miniaturize traction drives. In principle, the larger the force to press rollers against each other is, the larger the transmission torque becomes; however, pressing a roller with a strong force would rise the pressure on the roller’s contact surface too much, and shorten the life of the component itself. This is why it is mandatory for a traction drive to be large to some extent.
NIDEC DRIVE TECHNOLOGY solved this issue by improving the shape of its rollers to enable them to withstand an increased pressing force, and transforming the area of roller-to-roller contact from a point to a line, to disperse the pressing force. Furthermore, by performing computer simulation based on the FEM (finite element method) analysis, the company successfully optimized its traction drives’ structures and made their components strong enough to withstand high pressure. At present, NIDEC DRIVE TECHNOLOGY produces traction drives approximately the same sizes as those of gear reducers.
A traction drive 13dB quieter than a gear reducer
In 2016, NIDEC DRIVE TECHNOLOGY became the first company in the industry to develop S-CART, an automated guided vehicle whose running route can be set freely. Though its power is transmitted by a gear reducer, S-CART is gaining popularity with its wide range of lineup (Individual models can transport a load of up to 100kg, 200kg, 500kg, and 1t respectively). Recently, anticipating the need to assist luggage transportation work at hotels, the company has developed hotel-dedicated unattended carriages, which can carry luggage and follow hotel staff and guests. Using traction drives for these hotel-use S-CART units, NIDEC DRIVE TECHNOLOGY is planning to expand the product’s sales for hotel applications.
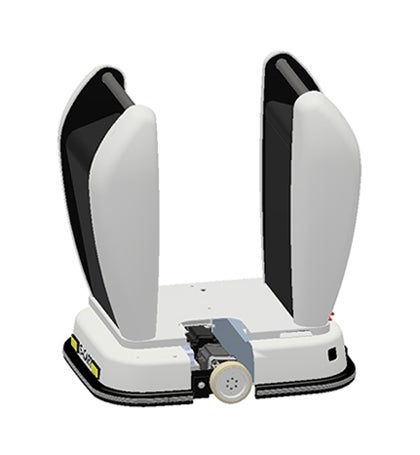
A noise comparison experiment using automated guided vehicles of the same chassis and respectively loaded with a gear reducer and a traction drive revealed that the noise from the one with a traction drive was 13dB lower than that of the other. The level of noise is low enough for people not to be bothered even if the vehicle ran inside a library – a result that promises the product’s sufficient marketability.
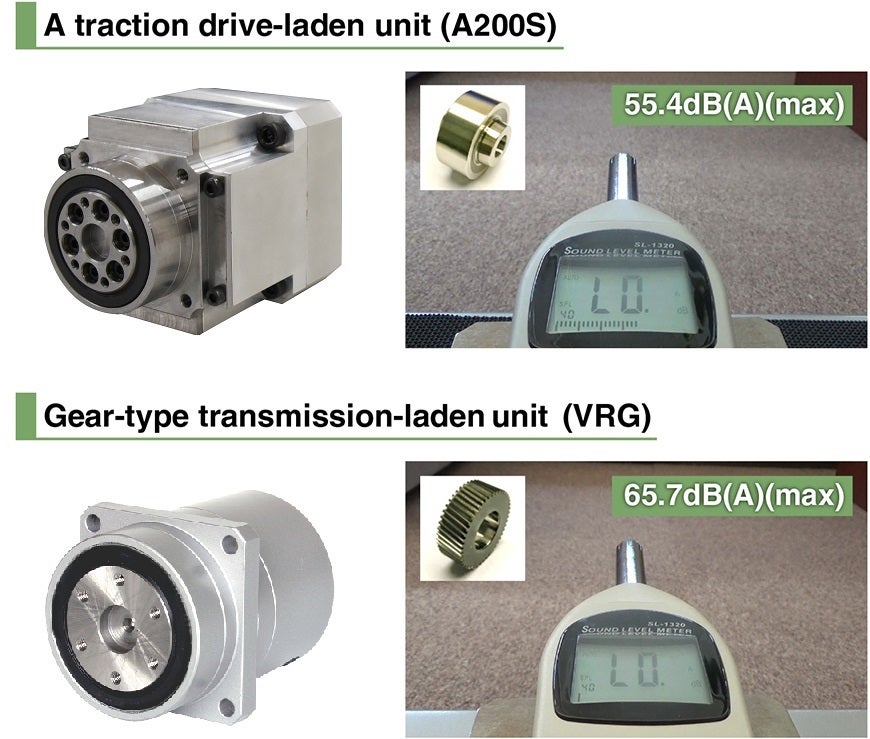
Now, after the S-CART passed an internal durability test in 2020, final adjustments are ongoing at NIDEC DRIVE TECHNOLOGY to launch mass-production finally. In the meantime, the company is bracing itself to constantly try to make the product smaller and quieter, to produce a traction drive that is more compact than a gear reducer, and quieter than a rotating motor, in the future.