NIDEC's Technical Capabilities
Fundamental Technology for Innovative Motors
Higher torque density, less noise and reduced vibration—laying the foundation for the motors of tomorrow
One of the applications of our products that has attracted much attention recently is service robots. In contrast with their industrial counterparts used in factories, these robots are at work in everyday locations such as households and hospitals. The motors used in service robots are required to be thin, compact, quiet and achieve high torque output.
Nidec's axial flux motors fulfill these requirements as they are thin, have high torque output and are capable of gearless direct drive due to their vertical alignment of the magnet and the iron core, setting them apart from conventional radial flux motors. In order to overcome the vibration and noise problems inherent in high-torque motors we have not only paid special attention to the design of the supporting structure but also adopted structural designs and electronic control methods that reduce noise and vibration. For example, by placing the iron core diagonal to the axis and controlling the electric waveforms, torque ripple can be reduced, leading to less vibration and noise.
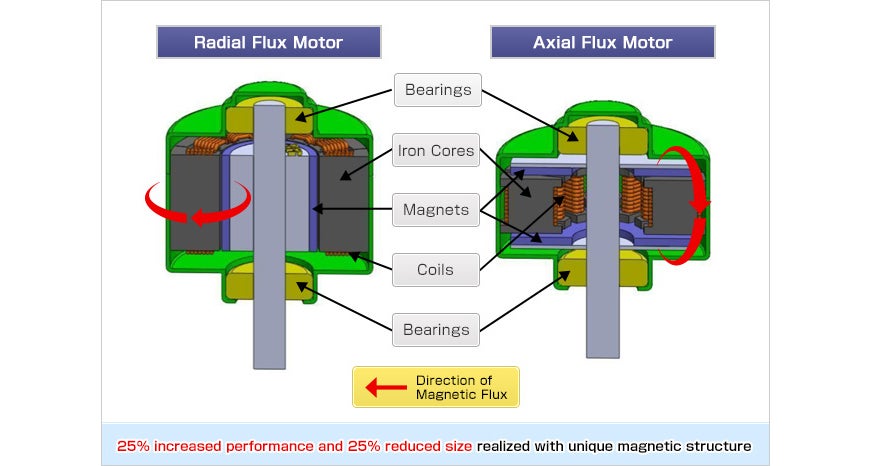
Flow dynamics, electromagnetism, acoustics as well as the structural aspects of the motor are taken into account and analyzed together in order to formulate effective strategies for reducing unwanted noise and vibration.
By analyzing the electromagnetic force working on the iron core, the vibrations propagating from the iron core to the housing of the motor, and the resulting vibration of the housing itself, can be visualized and interpreted. To allow for even more seamless composite analyses, we have developed our own interface tying multiple analysis software tools together. Using this interface makes it possible to combine a wide array of commercially available software tools specializing in flow, structure, thermal, acoustic, vibration, motion, electromagnetic analysis and more. For example, with these analytical tools at our fingertips, we can analyze the internal airflow and heat distribution of our fan products to develop optimally designed exhaust modules consisting of fan motors, cooling fins and heat pipes, as opposed to supplying single-unit ready-made fans. Recently, we have been supplying many similar custom products realized through active use of our in-house-developed interface combining multiple analysis software tools.
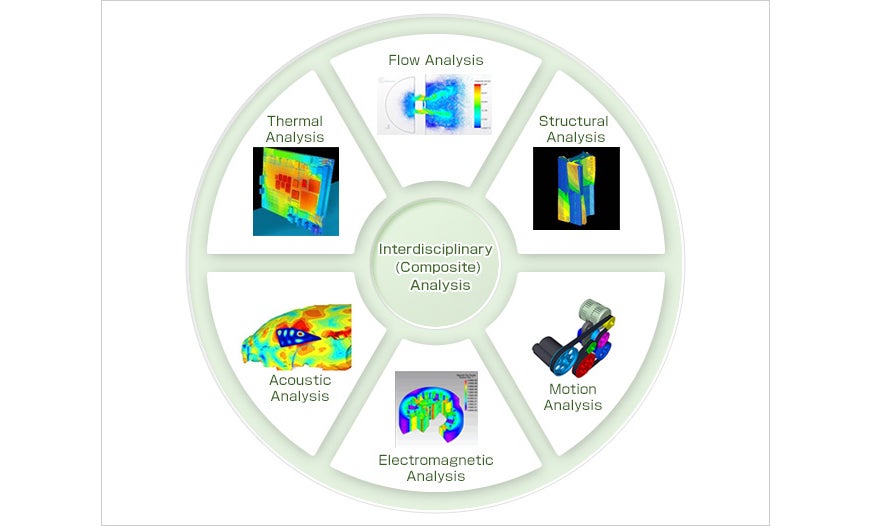
Traditionally, modules integrating fans, blowers, pumps and compressors with motors have been designed by combining various individually designed components during the testing phase of the development process. However, due to the increasing demand for products realizing conflicting design goals—such as compactness, high output, high efficiency, high controllability, exceptional product quality and low cost—system design approaches aiming to optimize entire units and modules combining motors, mechatronic components, sensors and controllers and have become necessary.
The method adopted by Nidec to address this shift is model based development—simulating digital models of the mechatronic components and control circuits etc that increase the load on interconnected motors in order to verify the validity of different module and unit functions. In this way, we achieve overall optimization by using supercomputers to refine motor design ideas before creating physical prototypes.
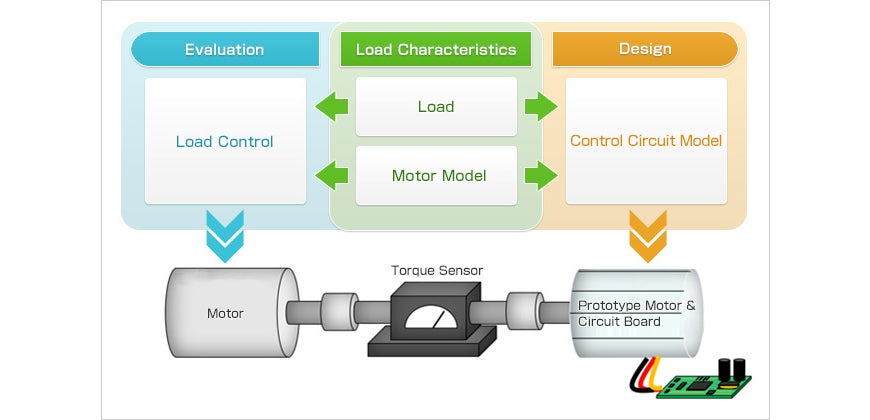