Supply Chain Management
Customer Relations
Basic philosophy
To meet the variety of customer demands, Nidec has a basic sales philosophy knows as “QCDSSS (Quality, Cost, Delivery, Speed, Service, and Specialization) ,” based on which development, production, and sales departments work in an integrated way to secure better customer satisfaction and build excellent customer-supplier relationships. To quickly answer the needs of our customers around the world, we exercise a “made in market” strategy, where we develop, produce, and sell our products close to our customers. This is how we stay close to the market in each region, providing speedy and detailed services that meet our customers’ needs.
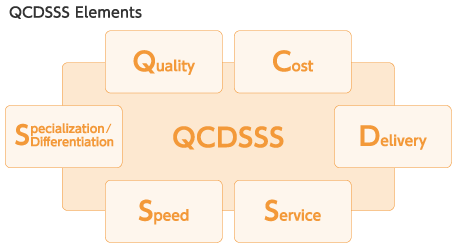
As a manufacturer featuring an extensive product line-up and large supply volume, Nidec has a duty besides simply providing products; we must ensure safety in every aspect, from the selection of parts in light of environmental friendliness to the safety of products, as well as disposal and recycling. We believe that we can help create sustainable social infrastructure by providing our customers with products that can be used in a safe and dependable manner. To realize this idea, it is necessary to maintain a high level of product performance in terms of environmental friendliness, requiring a database that serves as a guide to selecting materials at the time of component design. Moreover, now that the automotive products business has developed into a major segment accounting for over 20% of the Nidec Group’s consolidated net sales, in order to satisfy the quality needs of all customers in the automotive industry, it is important to establish a globally unified quality assurance system. And, Global Quality Management Division, an organization established to supervise the entire Nidec Group’s quality assurance function, works with individual Nidec Group companies & quality assurance departments to operate a group-wide quality management system.
Target
Materiality
Systems and actions
The Small Platform Motor & Solutions Business Unit, which operates businesses in environmentally advanced countries such as EU countries and has many customers with a high awareness of environmental issues, has already complied with current regulations. However, it is expected that legal regulations and social demands will become even stricter in the future, so we are working to reduce the amount of lead used in materials that are difficult to replace and to curb CO₂ emissions by recycling resin materials in advance of the laws, regulations and demands of each country. Specifically, we are promoting the replacement of steel materials used in products for some customers with low-lead materials. We are making proposals, particularly to customers in the IT industry, and have received orders for low-lead materials for new products to be released in FY2023. In terms of promoting the use of recycled resin materials, we have proposed and shipped products that has increased the use of recycled resin materials to 50% to some customers, and we are currently evaluating the characteristics of these products, including their reliability. Toward the future, we will continue to develop products that use recycled resin materials and promote these to our customers.
Meanwhile, in the Automotive Motor & Electronic Control Business Unit, where quality requirements are even stricter, we are working to ensure high product and process quality through the Quality Management audit of project deliverables conducted by the Quality Assurance Department in the development of new projects. We have introduced a system in which the Quality Assurance Department, which is an internal third party, carefully examines and evaluates the deliverables (project tasks) of all departments. This initiative is implemented in line with the project plan, and by obliging the reporting of results to top management, we are improving the quality of product development and strengthening activities to prevent product safety risks within the Automotive Products Division.
The global quality management division, which was established as a cross-sectional function to oversee quality across the entire company, holds regular meetings attended by the quality assurance departments of each NIDEC Group company, and works to understand the quality situation at each company and share best practices across the company. In the product development flow of the entire NIDEC Group, we are promoting the maintenance of standard documents that guide basic quality assurance practices, from understanding customer requests to product and manufacturing process design, and after-sales service after mass production, and ensuring that these are thoroughly implemented in each business entity.