E/Environment
Contribution to Environment through Products and Solutions
With its environmental philosophy, “With a keen awareness that ongoing conservation of the global environment is a task common to all humankind, we will fulfill our social responsibilities by working to reduce environmental load by carrying out eco-friendly business activities,” the Nidec Group considers it to be a critical mission to offer, through our business activities, products and solutions that solve environmental issues.
The Nidec Group’s high-level manufacturing capability
It is said that about half of the electric power generated in the world is consumed by motors. Currently, most of these motors are energy inefficient motors such as AC motors and brushed DC motors. Seeking to produce more efficient and sophisticated motors, and by demonstrating our high-level manufacturing capability of light, thin, short, and small products, the Nidec Group is poised to develop and provide products and solutions that contribute to reducing society’s environmental load by, for example, reducing electricity consumption and materials to use. We also provide solutions that support the spread of renewable energy, and play a role in global energy conservation and decarbonization.
Contribution to society and the environment through low-carbon and decarbonized product
In providing the world with products that contribute to society and the environment, the most important thing is the basic design of the product. We have been working on reducing materials used for a long time by making them lighter, thinner, and smaller. In addition to contributing to energy savings during customer use by improving energy efficiency, other important factors include reducing energy consumption during product manufacturing and selecting low-carbon materials. In addition, we must pay attention to reducing the environmental load of a product’s overall lifecycle, as some products achieve a significant CO₂ emissions reduction during their use phase even though they emit CO₂ during their manufacturing phase. So far, Nidec has had in place a system to quantify, as the “amount of avoided emissions*1,” the effect of CO₂ emissions reduction during the use phase of EV traction motor system E-Axle and other automotive motors. In addition to the system, for other phases of lifecycle as well, we used the lifecycle assessment (LCA)*2 to build a carbonization-based environmental impact assessment method, and started quantifying individual lifecycle phases’ CO₂ emissions.Establishing an environmental impact assessment method enables us to quantify the “amount of our reduction contribution” in a comparison of our conventional products, and to launch actions for further CO₂ emissions reduction. Going forward, we will stay committed to producing light, thin, short, and small products, and enhance their efficiency to reduce product-based CO₂ emissions.
※1 "avoided emissions" at the stage of use of automotive motors is quantitative targets are disclosed in materiality initiatives. About materiality initiatives here. Please see the page.
※2 Life Cycle Assessment (LCA) is a method to quantitatively assess potential environmental impacts on the earth and ecosystems during the life cycle of a product, from procurement of raw materials to disposal or recycling.
Nidec’s high-efficiency, light, thin, short, and small products
Automotive Motors
Traction motor system "E-Axle"
In anticipation of decarbonization, we started mass production of the E-Axle traction motor system for electric vehicles in 2019. An electric vehicle uses a motor to convert electricity into driving force, so it does not emit CO₂ when the vehicle is in operation.
EPS Motors
The key to reducing CO₂ emissions from vehicles with internal combustion engines is to reduce the load on the engine and improve fuel efficiency. To improve fuel efficiency, the adoption of EPS (electric power steering) is progressing along with an increase in idling stop vehicles that stop the engine when the vehicle is stopped and an increase in hybrid vehicles (HEVs) that can run with the engine stopped. By replacing hydraulic power steering with EPS, it is expected that fuel efficiency will improve by about 5%.
DCT Motors
A trend is emerging in Europe and China where the DCT (dual clutch transmission) system, which is as operable as the AT (automatic transmission) system and yet capable of improving fuel-efficiency performance, is chosen to be used in vehicles. Compared with the AT system, the DCT system can improve fuel efficiency by approximately 9%.
Electric oil pump motor
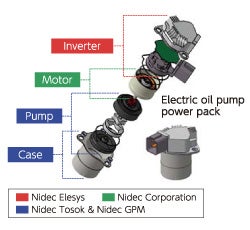
The idling stop function, which stops the engine when the vehicle is parked, temporarily stopped, waiting for a traffic light, etc., can improve its fuel efficiency by approximately 5 – 8%. Realizing this improvement requires an electric oil pump motor, which can maintain the hydraulic pressure of the transmission in the engine when it stops.
The Nidec Group supplies automobile manufacturers with groups of products that effectively improve fuel efficiency, and that help curb CO₂ and air pollutant emissions.
SR Motor for Large Vehicles
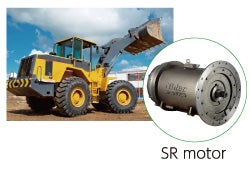
The Nidec Group, in addition to other motors, develops and produces SR (Switched Reluctance) motors*, which are used, instead of conventional engines, to drive construction equipment, mining & agricultural vehicles, and other industrial vehicles. Industrial vehicles’ operating sections function by hydraulic pressure, and an engine is installed in these vehicles to enhance it. The SR motor accumulates the electricity generated by such an engine in a battery, and utilizes the electricity, spending energy very efficiently. This is how SR motors significantly save energy and reduce CO₂ emissions when vehicles operate.
*SR (Switched Reluctance) motor: Motor that does not use magnets (rare earth-free).
Inverter Air Conditioner Motor
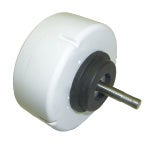
The inverters, installed in air conditioners, which are used in growing numbers worldwide, control their motors’ rotating speed, save energy significantly, and control air volume, helping air conditioners evolve into energy-saving, low-noise, and comfort-conscious products.
The brushless DC motor, one of the Nidec Group’s flagship products, is an essential component in these inverter air conditioners. Producing these motors in China, Thailand, and many other parts of Asia, we modularize them with blowing motors and inverter circuits to make high-performance motors, which are delivered to air conditioner manufacturers worldwide, while helping individual countries to reduce their electricity consumption.
High-performance Motor that Meets the IE3 (Premium Efficiency) Regulations
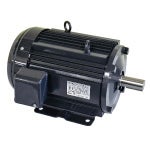
In Japan’s industrial sector, approximately 75% of electricity produced is estimated to be spent on motors. If Japan’s industrial motors, almost all of which are currently at the IE1 (standard efficiency) level, were to be replaced entirely by IE3-level (premium efficiency) motors, it is estimated that a significant amount of power would be saved – 15.5 billion kWh per year, and such savings would also be effective for many other countries in the world.*1 The Nidec Group has been producing the “NEMA Premium Motor,” an industrial motor that meets the US’s NEMA*2 standard (equivalent to IE3), since 2011, and started, ahead of the regulations, the supply of IE3-level motors in September 2014. Furthermore, we have already developed advanced IE4- and IE5-level motors as part of our efforts to dramatically improve the energy efficiency and CO₂ emissions reduction records of the world’s industrial equipment.
*1: Source: Japan Electrical Manufacturers' Association "Top Runner Motor"
*2: National Electrical Manufacturers Association
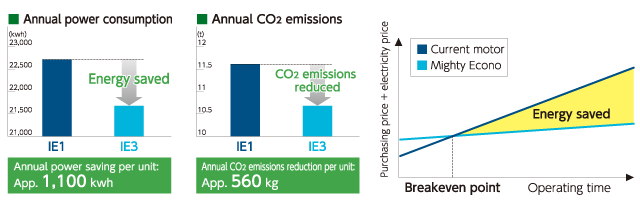
The above chart is based on an energy-saving and CO₂ emissions assessment of Nidec Techno Motor Corporation’s “Mighty Econo” motor (IE3 level), in which the energy-saving effects were calculated based on a scenario where a 7.5 kW, 4P, 50 Hz motor was operated for 10 hours a day and five days a week for a year. More energy will be saved with more units operated for a longer period of time.
Providing Renewable Energy Systems
Contributing to Realizing a Stable Power Supply and a Low-carbon Society
Nidec ASI, a company that handles everything concerned with renewable energy – from power generation to storing to transmission and distribution – offers system solutions to supply low-cost power reliably and stably to both large-scale facilities such as hospital and shopping malls, and remote places such as small regional villages.
The company smart micro-grid project integrates photovoltaic, wind, and other power generation systems with batteries, successfully developing a micro-grid technology that ensures optimum power management. Using this technology, Nidec ASI delivers stable power to various areas in the world where power supply has been unstable.
In its BESS (Battery Energy Storage System), Nidec ASI has developed and offers a power storage system that temporarily stores surplus electricity in a regional power network, and releases the electricity when power supply becomes unstable, to ensure stability of the power supply.
![]() Micro-grid system in Chile |
![]() BESS (Battery Energy Storage System) system in Germany |
Photovoltaic power generation plant in a suburb of Ciminna, Sicily, Italy
Project Report
Smart Micro-grid Solution
In this project, we installed a large-scale power storage system in the village of Ollague, located 3,660 meters above sea level in the Andes Mountains which run through Chile in South America, to supplement the electricity generated by solar, wind, and other energies, which were unable to provide a stable supply. In addition, we launched a new project to integrate the existing diesel power generators with our new system, to provide a stable supply of electricity.
Now, with the necessary power supplied constantly, 24 hours a day, people in the Ollague village are able to read even at night, while TV sets, refrigerators, and other appliances are starting to be used widely in the village.
Reducing CO₂ Emissions in the Ore Business
In June 2023, Nidec ASI signed a contract to install the largest BESS in a mine in South Africa. Electricity generated by the solar power plant is stored in a total of 120 MWh of battery, providing a stable supply of electric power. The BESS installation will be able to handle the mine's average daily power supply, saving around 200 tons of CO₂ per 120 MWh cycle. We will not only realize a stable power supply at mines, but also contribute to the expansion of the use of safe renewable energy.