Laser・Semiconductore manufacturing equipment・Metal additive manufacturing|3D metal additive manufacturing machines|Powder DED 3D metal additive manufacturing machines
Powder DED 3D metal additive manufacturing machine LAMDA
The handling companies : Nidec Machine Tool Corporation
- Contact information for product inquiry
- Contact us
Metal 3D Printer using the powder DED method which supports modeling of large parts

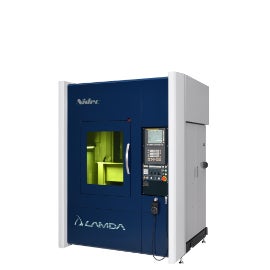
LAMDA200
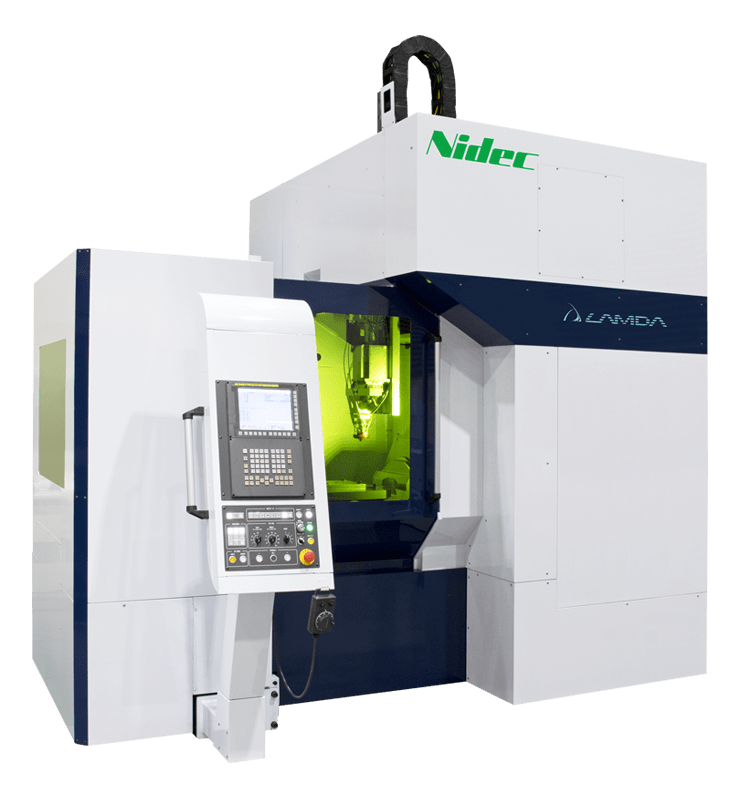
LAMDA500
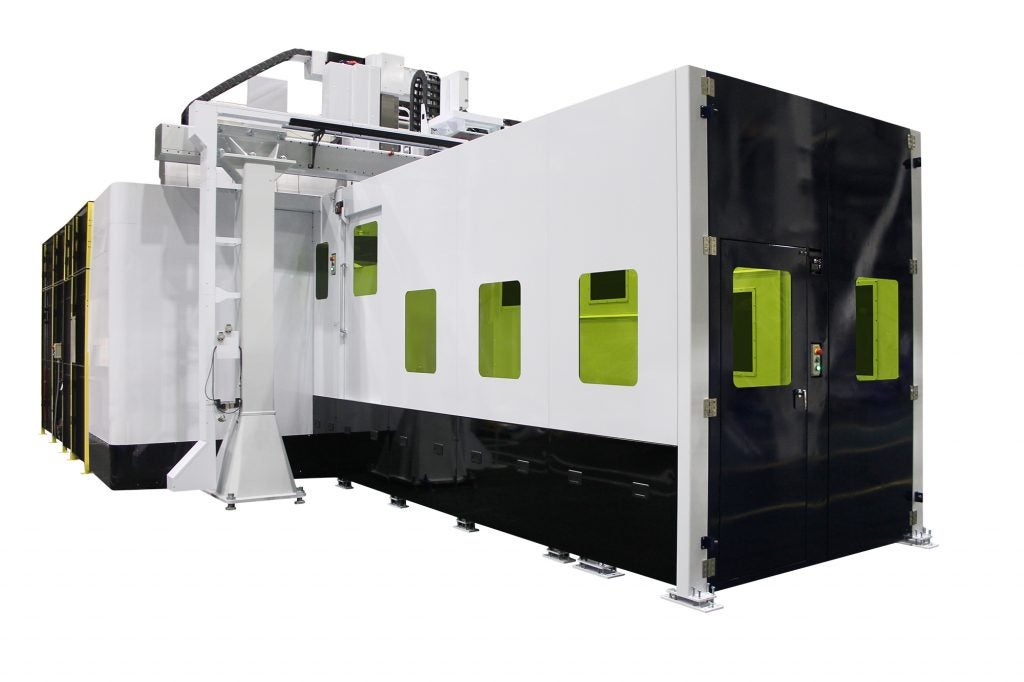
LAMDA2000
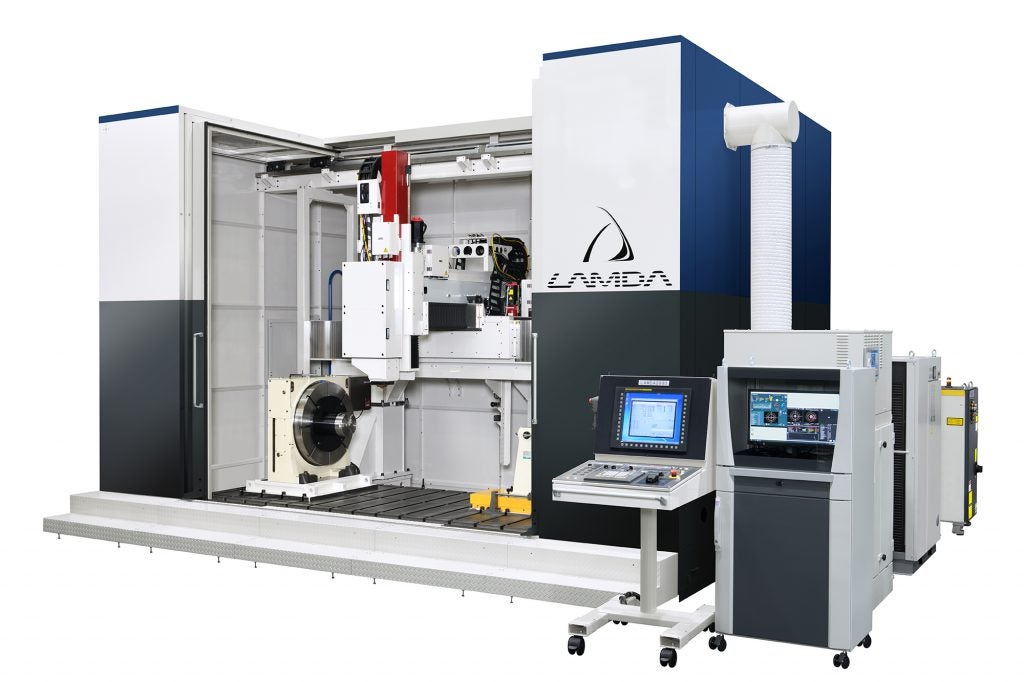
LAMDA2000
Features
Local shield
Using local shield gas that prevents air flowing into the melt pool, it makes possible to shape materials that dislike oxidation, such as titanium alloys, in the atmosphere.

Quality improvement of additive manufacturing
The feedback function stabilizes the state of the melt pool and improves the quality of additive manufacturing.
The monitoring function records the status of the melt pool and ensures quality traceability
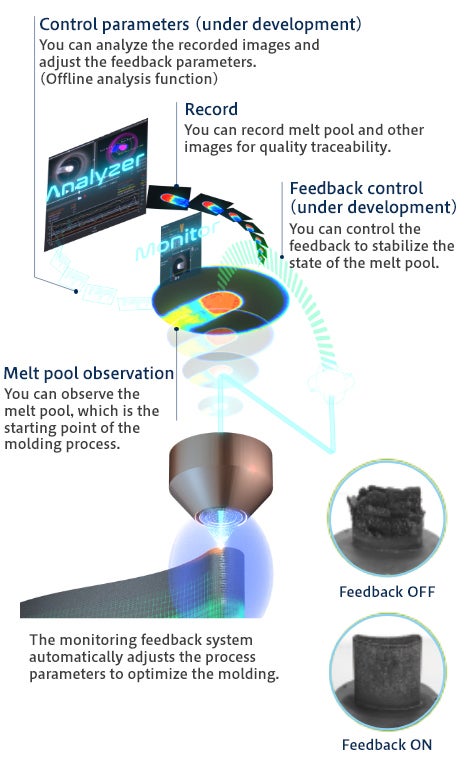
Case Study
Modeling from near net shape
If it is premised on overlaying with DED, you can use a material with a near net shape (dimensions close to the final shape).
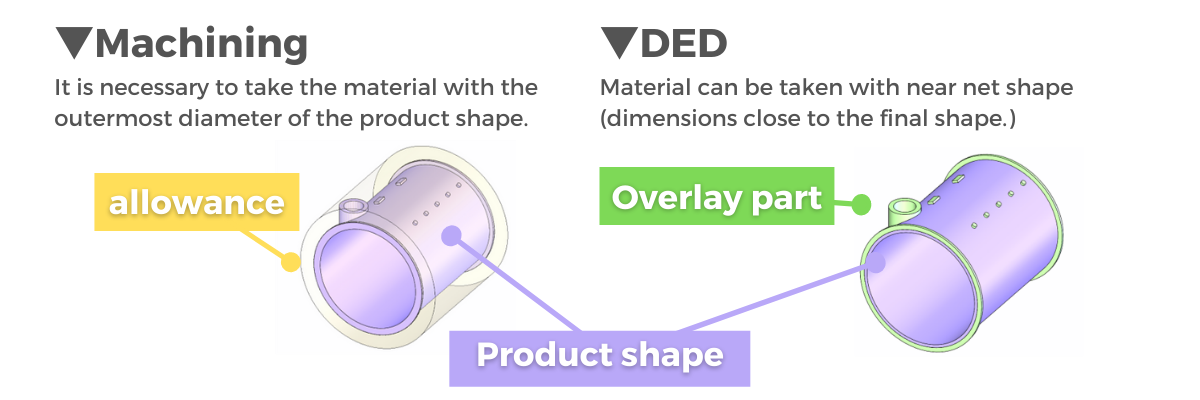
・In the case of cutting, the material is taken and cut at the outermost shape of the product shape.
There is a lot of cutting margin, and the cutting time is especially long for difficult-to-cut materials. It also costs a lot of material costs.
・When using DED, use the "near net shape" material that minimizes the shaving margin, and build up to finish the product shape.
Delivery time can be shortened by modeling and cutting only the necessary parts. Material cost can be reduced by thinning.
Efficiency of high-mix low-volume production
If you need similar shape variations of parts, you can streamline their production.

・In the case of a construction method in which a casting mold is manufactured according to the final shape, each mold is required even if only a part of the shape is different.
The delivery time of the material will be longer, and it will be difficult to handle the production of special shapes.
・When using DED, each flange part is modeled based on the basic shape. It is OK to prepare only the minimum necessary casting mold.
If the material has a simple shape, the delivery time can be shortened. At the same time, it becomes easier to handle variations in the shape of parts.
Specifications
format | LAMDA200 | LAMDA500 | LAMDA2000 | LAMDA2000 |
---|---|---|---|---|
Maximum modeling size (mm) | 200×200×200 | 500×500×500 | 2,000×1,500×1,600 | 2,500×900×1,000 |
Laser output (kW) | 1・2・4・6 | |||
Number of powder supply pots | 1・2 | |||
Inert gas shield | Applicable | |||
spindle specifications | N / A | Applicable | N / A | |
NC axis table | Applicable with 1-axis and 2-axis tables | 2 -axis tablestandard | Applicable with 1-axis and 2-axis tables | |
Jig cooling | Applicable | |||
Machine size (installation space) (mm) | 4,000 x 2,600 | 4,000 × 6,000 | 12,000 x 6,500 | 7,000 x 5,500 |
Mechanical mass (Kg) | 2,500 | 11,000 | 44,000 | 12,000 |
For other sizes, please contact the following inquiries.
This product is the result of the technology development project entrusted by the New Energy and Industrial Technology Development Organization (NEDO) to the Next Generation 3D Laminated Modeling Technology Development Organization (TRAFAM), Nidec Machine Tool Corporation It was developed by utilizing (formerly Mitsubishi Heavy Industries Machine Tool Co., Ltd.).