Machine Tools|Lathe|Combined Machining CNC Lathe
TMM-250M1Turret Type, 4-axes Multi-Tasking Machine
Company: Takisawa Machine Tool Co., Ltd
Milling and Y-axis control realize highly efficient process integration. Module-1 contributes to high productivity.
Moreover, Module-1 contributes to high production by automation.
- High value added production by process integration
- Module-1 is equipped with upper and lower 15-station milling turrets as standard which can perform turning and rotating-tool cutting. Milling is performed by 4000 min-1/5.5 KW milling power and Y-axis control. The upper and lower 15-station milling turrets provide stable machining accuracy by the index device having high repeatability and excellent centripetal feature.
- Contact information for product inquiry
- Contact us
Product's data
Machine Main Specifications
TMM-250 M1 | ||
---|---|---|
Upper Turret | ● | |
Lower Turret | ● | |
Chuck Size | inch | 10+8 |
Type of Turret | 15-Station Turret(T15) | |
Max. Turning Diameter | mm | φ350 |
Max. Turning Length | mm | 800/200 (Flange) |
Bar Capacity(Left Spindle) *1 | mm | φ76.2 |
Bar Capacity(Right Spindle) *1 | mm | φ50.8 |
Left Spindle Speed | min-1 | 4000 |
Right Spindle Speed | min-1 | 4000 |
Rotary Tool Speed | min-1 | 4000 |
Rapid Traverse Rate (Upper Turret) | m/min | X1 : 24 / Y : 12 / Z1 : 30 |
Rapid Traverse Rate(Lower Turret) | m/min | X2 : 24 / Z2 : 30 |
Left Spindle Motor(30 min/continuous) | kW | 22/15 |
Right Spindle Motor(30 min/continuous) | kW | 18.5/11 |
Rotary Tool Motor(S3 25%/continuous) | kW | 5.5/3.7 |
Machine Height | mm | 2250 |
Required Floor Space | mm | 4745×2932 |
Machine Weight | kg | 8500 |
●: Standard
*1) Please note the bar capacity follows types of chucks and cylinders.
TMM-250M1G Process Integration + Automation
Loader Specification
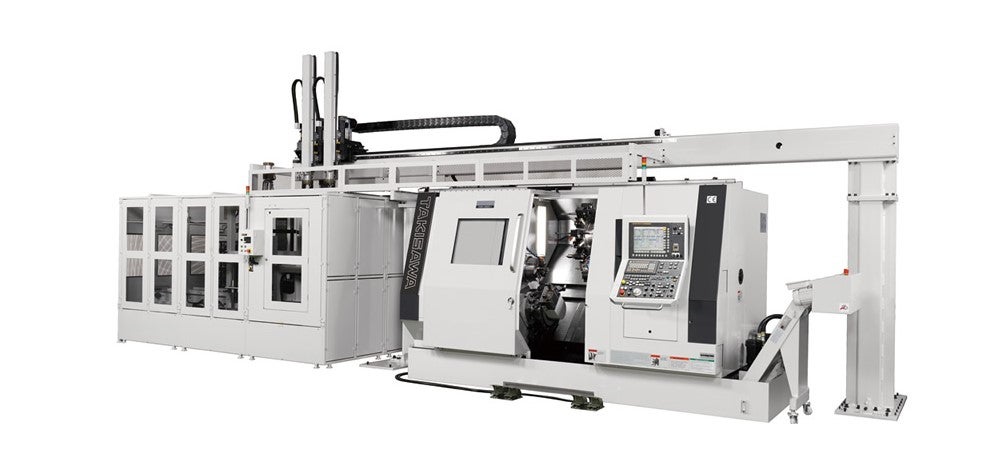
Takisawa Original Software Tiwap-1(Optional)
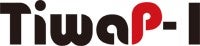
"TiwaP-1" is an interactive programming system fully supporting creation, simulation, and execution of machining programs to reduce operator' labor.
"Input" by the interactive system is easy for the operator to create programs without knowledge of G codes. "Check" of programs can be done by simulating the cutting results with 3D animation and tool path drawing. In "Operation", the machining spindle and the order of process types are automatically recognized to optimally execute spindle control and C-axis zero return.
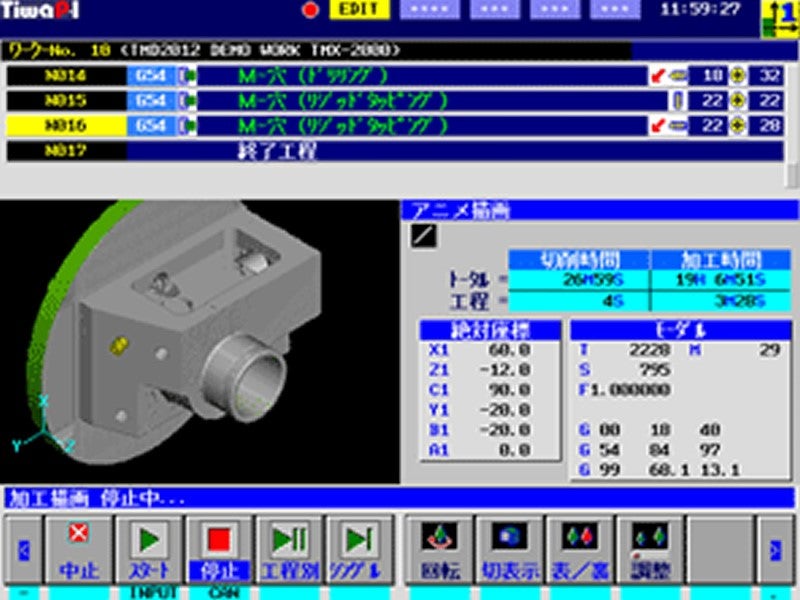