Influence on hob tool life against heat treatment of pre-hobbing materials
In hobbing, the tool wear may vary even under the same cutting conditions.
One of the causes may be the effect of work material hardness or heat treatment.
Here is a survey on hob tool wear due to differences in work material hardness and heat treatmentfor your reference.
Case 1) Workpiece structures (particle size) are different
Particle sizes are different due to heat treatment variations and this causes the difference of the tool wear.
Annealed material has higher hardness with larger grain size than Normalised material, resulting in less tool wear.
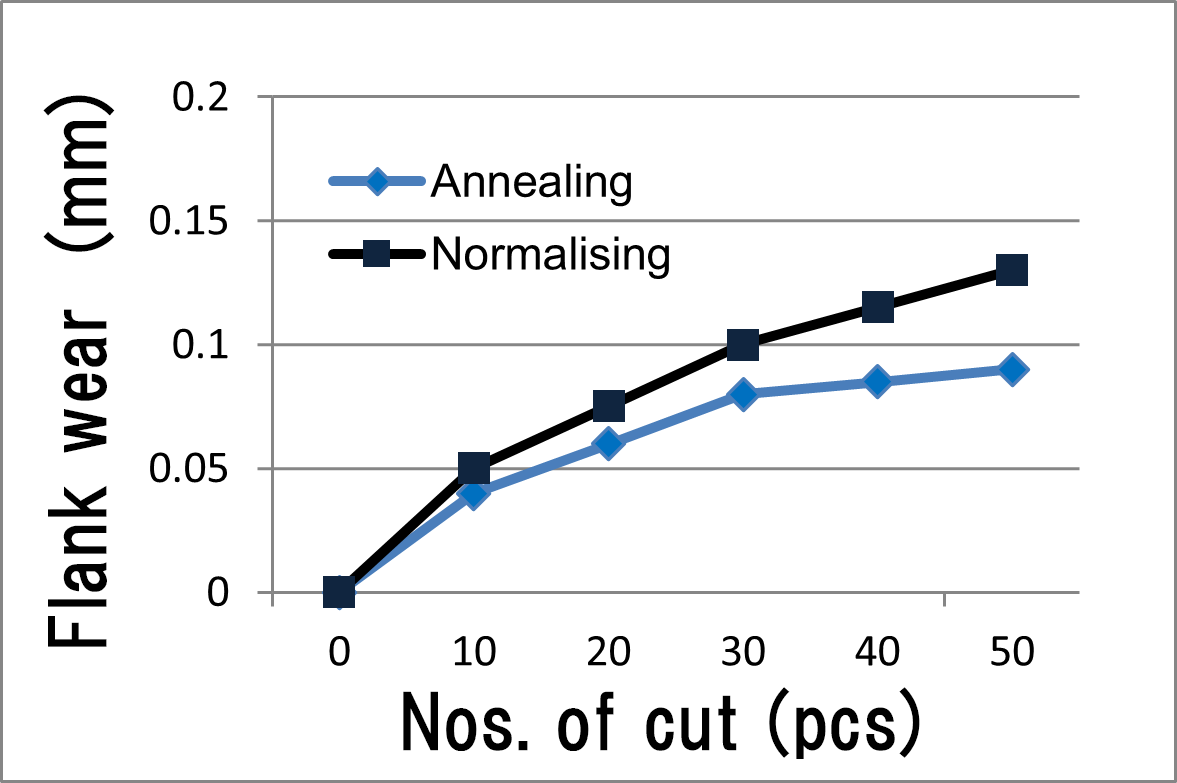
Annealing | Normalising | |
---|---|---|
![]() | ![]() | |
Particle size number | 6 | 8 |
Hardness | HB168 | HB155 |
Material | SCM420H |
Case 2) Workpiece structures (particle size) are not significantly different
Particle sizes are not so different even the heat treatment variations and this causes not much difference of the tool wear.
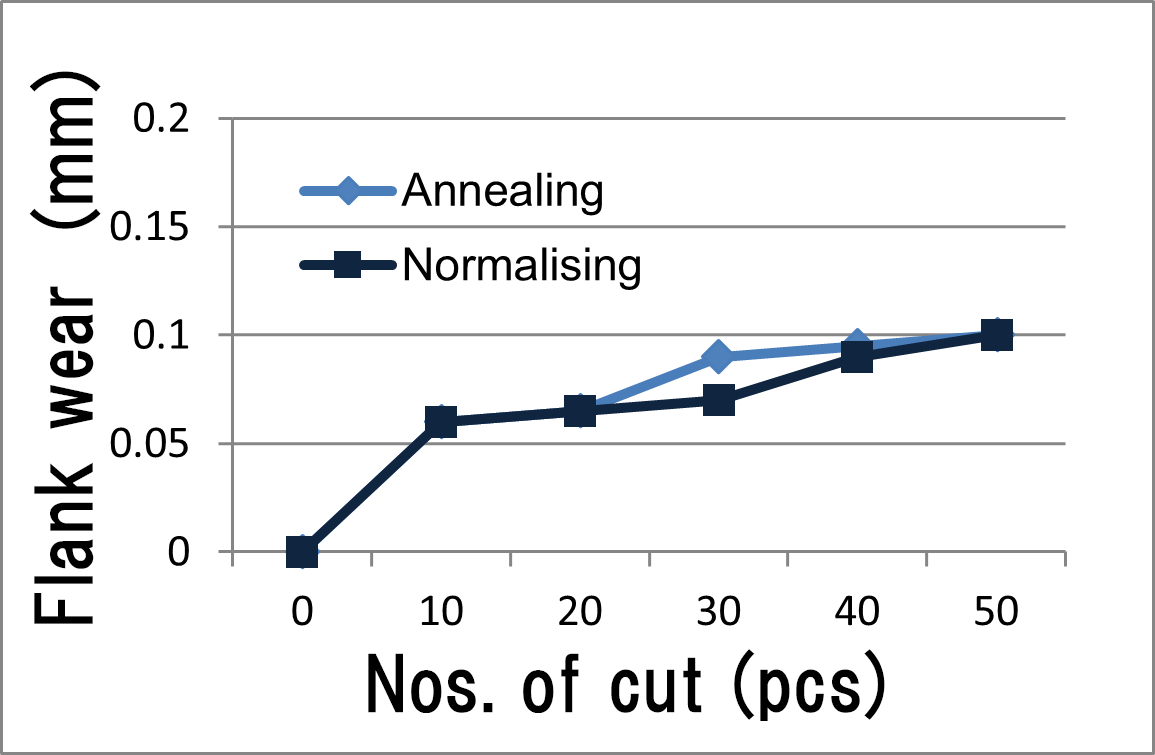
Annealing | Normalising | |
---|---|---|
![]() | ![]() | |
Particle size number | 7 | 8 |
Hardness | HB168 | HB169 |
Material | SCR420H1 |
- Workpiece Spec: m2.25 PA17.5°52T 23°LH OD135 Material:SCR420H1,SCM420H
- Cutter Spec: OD75 L150 3starts 16flutes Material MACH7(HSS) Coat SuperDry PVD
- Cutting condition : V=230m/min f=2.4mm/rev Machine GN20A DRY CUT 50pcs cut , no-shift