AIKITEC CO., LTD.
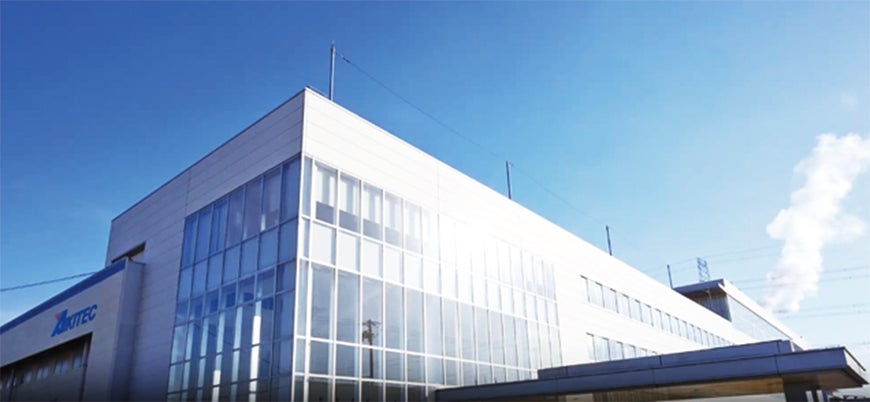
Since its founding in Showa 31, AIKITEC CO., LTD. has been manufacturing transmission and engine parts, which are important functional parts for motorcycles and automobiles, with gear processing as its core technology. Centered on the head office factory in Aichi Prefecture, we are now expanding globally to the United States, China, and Indonesia.
AIKITEC's factories in Japan and overseas have delivered more than 100 units of NIDEC equipment, including gear grinding machines. In 2023, we introduced the newly developed CF26A Cutting Chamfer System. This time, we asked about the background to the introduction of the new construction method and future initiatives.
An automotive parts manufacturer boasting an integrated production system from forging to finishing
Q: What are your strengths?
General Manager Narita: Since our founding, we have been manufacturing automotive parts for a living. Based on our many years of experience, we are demonstrating our strengths as a supplier that can supply high-precision precision vehicles with the same quality globally based on our core technologies such as precision forging technology and surface finishing technology. In particular, we have been mass-producing and supplying gears for more than 25 years, and we have a wealth of experience and knowledge, and we have earned the trust of many customers.
Q: Please tell us about your company culture.
Mr. Narita: We established our purpose two years ago with the aim of clarifying the significance of our existence, such as how to survive in the automotive industry, where the external environment is changing drastically, and what kind of activities we should pursue as a company from the perspective of CSR.
Senior Managing Director Kawabata: Our employees always carry a leaflet with our purpose written on it in their breast pockets. "Bringing smiles to the future" has another meaning, as well as making everyone smile in the future. We have been in the automotive industry for a long time and have been involved in CO2 emissions. It may be difficult to stop it now, but it also contains the meaning of the SDGs, which is to stop it at some point so that we can smile in the future. This purpose was conceived by about 10 people of various ages from each department.
Q: You have many production bases overseas
Senior Managing Director Kawabata: We mainly produce automobile parts in North America and China, and in Indonesia, we also produce motorcycle parts locally in addition to automobile parts. The concept of production is basically "local production for local consumption". When we receive a job for a large project, we will set up a local production base. However, there is no guarantee that the project will last forever. I'm always on the lookout for another new job there.
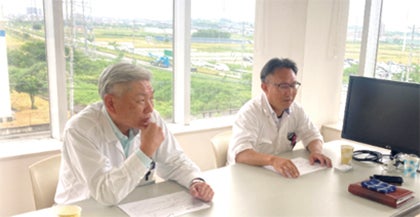
Right: Mr. Narita, General Manager, Sales Purchasing Department, Sales Division
Chamfering accuracy has become stricter. I want to internalize new technologies with little investment!
Q: Please tell us how you came to rent and introduce the newly developed CF26A cutting bevel.
Senior Managing Director Kawabata: Until now, the chamfering process has not been fussed about accuracy, but gradually it is being instructed numerically on the drawings, and it is becoming difficult to respond with conventional processing methods (phrasing processing). Since phrasing is a plastic process, it is not a processing method that can aim for precise numerical values. When I was in trouble, I saw CF26A Cutting Chamfer at JIMTOF (*Japan's largest machine tool trade fair).
At that time, there was a problem that the phrasing cutter did not penetrate to the bottom of the tooth with shaft gears. In addition, ring gears had another challenge: the amount of chamfering was too large to be met by conventional phrasing.
Is the cutting chamfer perfect for these gears? So, I decided to introduce it by rental first.
The reason why I rented it was that it was still too early to buy. There was a movement to internalize this technology at an early stage with a small investment.
Mr. Narita: Even if we were to conduct processing tests, I thought it would be better to have a machine at hand than to test each time at Nidec's factory.
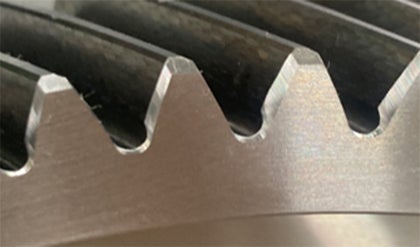
Q: Please tell us what made you decide to purchase the property after renting it for one year.
Mr. Narita: After delivering the prototype using a rental machine, the customer asked, "What kind of thing is a cutting chamfer?" and two companies actually came to see the actual machine. We started with rentals, but in reality, there are drawings that can only be processed by cutting chamfering. This is the reason why we decided to buy a rental machine.
Around the same time, we received a new order from a major transmission company in North America that required a cutting chamfer. Due to local demand, we decided to purchase a new CF26A for North America as well.
Q: Will the need for the CF26A increase in the future?
Mr. Narita: I think there will be a clear increase in needs. In addition to the problem of shape accuracy, the elevation of the tooth surface is also an issue in conventional phrasing. Recent gears are increasingly equipped with gear grinding finishes. Since the swelling caused by the phrasing process affects the deterioration of the tooth shape and the life of the grinding wheel, I think that cutting chamfering will be useful.
Senior Managing Director Kawabata: I still don't know if CF26A is the best of the "cutting chamfering" method. Originally, the chamfering process is a process that does not add value. We believe that it is best to have equipment with high cost performance accordingly.
If it is premised on automation, it saves space. It would be nice if it could be integrated with the hobbing machine like phrasing.
Mr. Narita: The CF26A is a machine that has just been developed. Since cutting chamfering is a processing method with a low load, there should be more money for improvement in the structure of the machine, the design concept of the mounting fixture, the shape of the chamfer cutter, etc. I believe that by making honest improvements, we will be able to gain a firm position as a processing method, and I have high hopes for that.
Senior Managing Director Kawabata: I think that the completion of development is not a goal, but a start. How can this method be disseminated? I would like you to think carefully and make Nidec's "CF26A" the de facto standard.
I want to take on new challenges in new fields.
Q: Please tell us about your future business.
Senior Managing Director Kawabata: For example, when dealing with European companies, we have switched to a trend in which prototyping must be done first before mass production can be achieved. As a company, we need to actively take on this kind of work, but for this we need to have the basic "technology," the "frontline" that gives shape to the technology, and the "sales" that we propose. I think it's important for everyone to work together.
Mr. Narita: In terms of the industry, we are in the process of promoting not only automobiles but also other industries that use gears, and exploring the second and third pillars after automobiles. Some projects are already in motion. We are developing our own G-BOX (reduction gear unit) that is used for e-Axles for "micro EVs" rather than competing with ordinary automobile-sized parts, not as a single component.
Q: The cars on display in the lobby are one of the new initiatives.
Mr. Narita: Yes, we would like to design and manufacture gearboxes in-house, and we would like to collaborate with Mr./Ms. manufacturers for motors and inverters to release products to the world as a unit.
Now that it is finally taking shape, we are delivering prototypes to customers and conducting in-house destruction and durability tests to achieve even greater heights.
Senior Managing Director Kawabata: We are still in the prototype stage, but we are working on the goal of launching the product on the market in the near future.
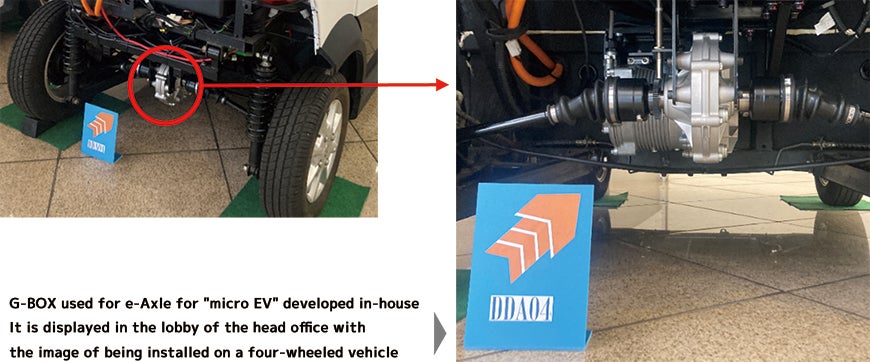
We received valuable opinions and impressions on the newly developed Cutting Chamfer CF26A. In addition, I was able to hear a story that made me think deeply about the company's business growth and product development as someone who works in the same manufacturing industry. We will make use of the opinions we receive in the next development and strive to provide better products and services.
AIKITEC CO., LTD.
〒470-2101 1-1 Sakaehigashi, Morioka, Higashiura-cho, Chita-gun, Aichi
TEL: (0562)82-3270
website:https://www.aikitec.co.jp/